The advent of Industry 4.0 represents a paradigm shift in manufacturing, characterized by pervasive digitalization, interconnectivity, and intelligent automation. Within this transformative landscape, the electric vehicle (EV) emerges as a critical focus, demanding continuous innovation in its core systems. Central to EV performance is the mechanical transmission system – the vital intermediary converting electrical energy from the motor into controlled mechanical motion at the wheels. My research focuses on identifying and implementing advanced optimization strategies for these transmission systems, leveraging the tenets of Industry 4.0 to enhance efficiency, reliability, and overall electric vehicle competitiveness.
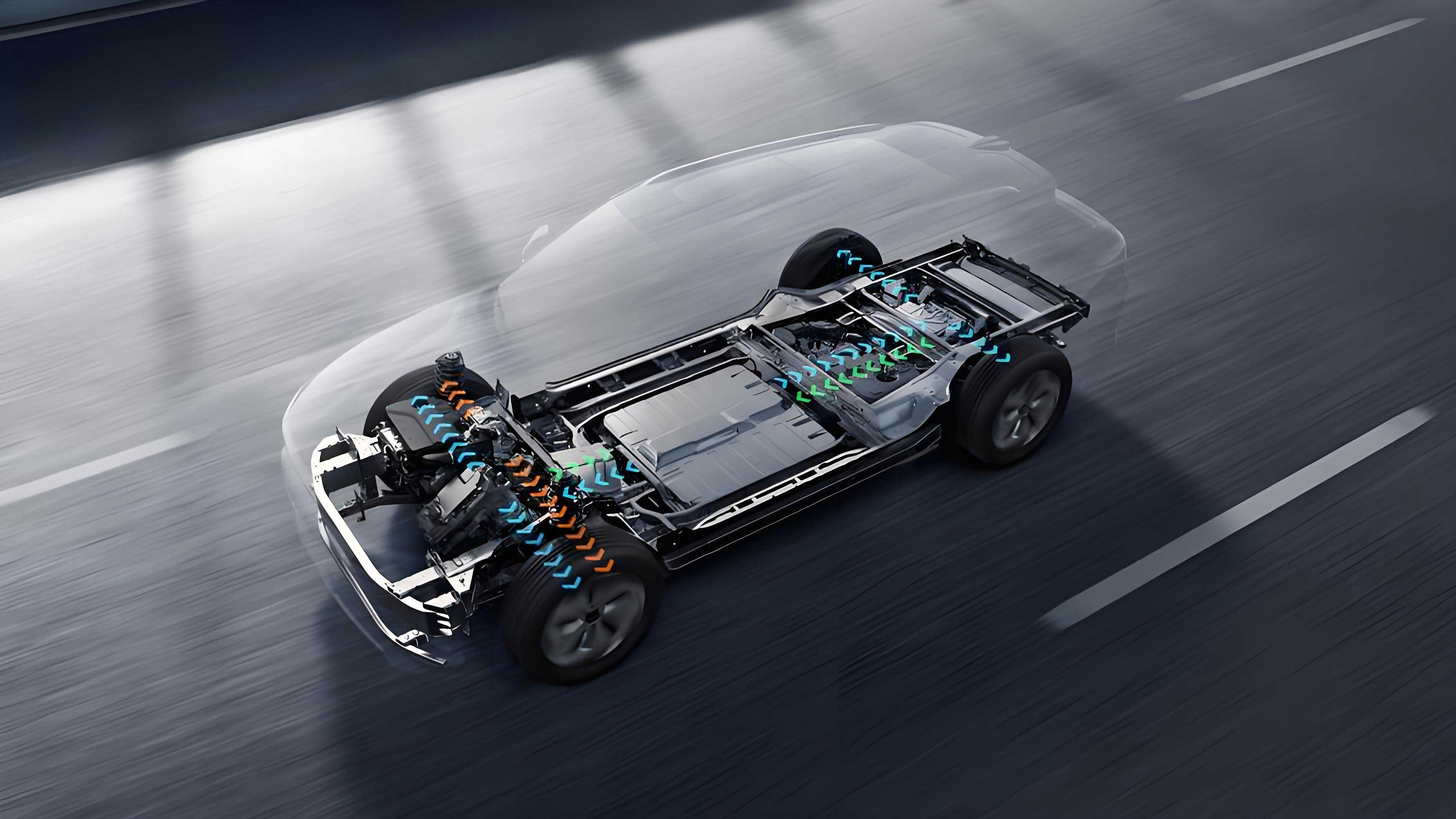
1. Industry 4.0: Reshaping Transmission System Development
Industry 4.0 transcends mere automation. It fosters the creation of “smart factories” where cyber-physical systems monitor physical processes, make decentralized decisions, and communicate seamlessly via the Industrial Internet of Things (IIoT). This creates unprecedented opportunities for optimizing mechanical transmission systems for electric vehicles.
Table 1: Core Industry 4.0 Technologies Impacting EV Transmission Design & Manufacturing
Technology | Impact on Transmission Systems | Benefit for Electric Vehicle |
---|---|---|
Digital Twins | Virtual replicas enabling simulation of performance, stress, wear, and NVH under diverse conditions | Reduced physical prototyping, accelerated design cycles, higher reliability |
Big Data Analytics | Processing vast operational data (temp, vibration, load) from sensors embedded in transmissions | Predictive maintenance, performance optimization, failure root cause analysis |
AI & Machine Learning | Optimizing gear geometry, material selection, control algorithms; enabling adaptive shift strategies | Enhanced efficiency, reduced noise & vibration, personalized driving experience |
Advanced Robotics & AM | Precision manufacturing of complex gear geometries; additive manufacturing of lightweight structures | Higher quality, reduced weight, novel material applications |
Cloud Computing | Centralized storage and processing of design, simulation, and operational data | Collaborative design, remote diagnostics, fleet-wide optimization |
The fundamental challenge lies in designing transmission systems that maximize the unique characteristics of electric motors – high torque at low speeds and wide operational ranges – while minimizing energy losses, weight, noise, vibration, and harshness (NVH). The equation for overall electric vehicle drivetrain efficiency (ηdrivetrainηdrivetrain) highlights the transmission’s critical role:ηdrivetrain=ηmotor×ηinverter×ηtransmission×ηfinaldriveηdrivetrain=ηmotor×ηinverter×ηtransmission×ηfinaldrive
Even minor improvements in transmission efficiency (ηtransmissionηtransmission) yield significant gains in electric vehicle range and performance.
2. Core Functions & Contemporary Challenges in EV Transmissions
Unlike internal combustion engines requiring multi-speed transmissions to operate efficiently across a narrow power band, electric vehicles often employ single-speed reduction gearboxes due to the motor’s broad torque curve. However, multi-speed transmissions are gaining traction for high-performance electric vehicles seeking optimized acceleration, top speed, and efficiency across diverse driving scenarios. Core functions remain:
- Torque and Speed Conversion: Adapting the high-speed, lower-torque output of the electric motor to the lower-speed, higher-torque requirements at the wheels.
- Direction Control: Enabling forward and reverse motion (often handled electronically within the motor controller, but mechanically managed in the differential).
- Power Transmission: Efficiently transferring mechanical power with minimal losses.
Table 2: Key Challenges in Modern Electric Vehicle Transmission Systems
Challenge | Impact on Electric Vehicle | Industry 4.0 Mitigation Strategy |
---|---|---|
Energy Losses (Friction, Churning) | Reduced driving range, increased battery demand & cost | Advanced lubricants, low-loss bearing designs, optimized gear microgeometry via simulation |
Noise, Vibration, Harshness (NVH) | Reduced driver/passenger comfort, perceived quality issues | Active vibration control, precision manufacturing, advanced acoustic simulation, optimized gear meshing |
Weight & Size | Reduced payload capacity, impacts vehicle dynamics & range | Lightweight materials (composites, alloys), topology optimization, integrated design |
Thermal Management | Overheating reduces efficiency, accelerates lubricant degradation & wear | Integrated cooling channels, smart thermal monitoring & control, advanced lubricants |
Durability & Reliability | High warranty costs, safety concerns, consumer dissatisfaction | Advanced materials (e.g., case-hardened steels, ceramics), predictive maintenance, robust design |
Cost | Impacts overall electric vehicle affordability and market penetration | Design simplification (where possible), advanced manufacturing techniques, supply chain optimization |
The pursuit of higher power density motors in electric vehicles intensifies these challenges, demanding transmissions capable of handling increased torque loads within constrained packaging.
3. Optimization Strategies Leveraging Industry 4.0
My research and implementation focus revolves around four interconnected strategic pillars:
3.1 Digital Design & Virtual Validation
Leveraging CAD (Computer-Aided Design) and CAE (Computer-Aided Engineering) tools is no longer optional; it’s fundamental. Sophisticated multi-body dynamics (MBD) and finite element analysis (FEA) software enable the virtual creation, testing, and refinement of transmission systems long before physical prototypes exist.
- Gear Optimization: Software like RomaxDESIGNER or MASTA allows precise calculation of gear tooth microgeometry (profile modifications, lead crowning) to minimize transmission error (a major NVH source) and optimize contact patterns under load. The basic gear mesh efficiency (ηmeshηmesh) can be modeled considering friction coefficients (μμ), normal load (FnFn), and sliding/rolling velocities (vsvs, vrvr):ηmesh≈1−μFnvsPinηmesh≈1−PinμFnvsWhere PinPin is the input power. Minimizing sliding velocity and friction coefficient is crucial.
- System Simulation: Simulating the entire driveline, including motor, transmission, shafts, bearings, and differential, under realistic load cycles (e.g., WLTP, US06) predicts efficiency maps, dynamic loads, bearing life (using standards like ISO 281), and NVH behavior. This enables holistic optimization impossible with isolated component design.
- Topology Optimization: Algorithms generate structurally efficient, minimal-weight component designs based on specified load paths and constraints, ideal for transmission housings and carriers. The objective function minimizes mass (mm) subject to stress (σ≤σallowableσ≤σallowable) and displacement (δ≤δmaxδ≤δmax) constraints:min(m)subject tog1(σ)≤0,g2(δ)≤0min(m)subject tog1(σ)≤0,g2(δ)≤0
Table 3: Digital Design Tools & Applications for EV Transmissions
Tool Category | Specific Software Examples | Primary Application in EV Transmission |
---|---|---|
CAD | CATIA, NX, SolidWorks, Creo | 3D Parametric modeling, Assembly design, Drafting |
CAE – FEA | Abaqus, ANSYS, Nastran | Structural stress/strain, Modal analysis, Fatigue life prediction |
CAE – MBD | Adams, Simpack, RomaxDESIGNER | System dynamics, Load prediction, NVH simulation, Bearing analysis |
CFD | Star-CCM+, Fluent, PowerFLOW | Lubrication flow, Churning loss prediction, Cooling analysis |
Topology Opt. | OptiStruct, Tosca, nTopology | Lightweight structural design generation |
Acoustics | Actran, VA One, LMS Virtual.Lab | Noise radiation prediction, Pass-by noise simulation |
3.2 Intelligent Control & Predictive Health Management
Embedding intelligence transforms passive mechanical systems into adaptive, self-monitoring components.
- Integrated Sensor Systems: Embedding sensors (vibration, temperature, torque, speed, oil condition) directly within the transmission provides real-time operational data. This is crucial for electric vehicles where transmission behavior directly impacts battery usage.
- Real-Time Control & Adaptation: Utilizing sensor data, control algorithms can adapt shift strategies (in multi-speed EV transmissions), clutch engagement (if applicable), or cooling flow to optimize efficiency or performance based on driver demand, terrain, and battery state. For example, optimizing shift points (NshiftNshift) to keep the motor operating near its peak efficiency region (ηmotor_maxηmotor_max).
- Predictive Maintenance (PdM): This is a cornerstone of Industry 4.0 value. By streaming operational sensor data to cloud platforms and applying machine learning (ML) algorithms (e.g., anomaly detection, regression models, neural networks), potential failures (bearing spalling, gear pitting, oil degradation) can be predicted significantly before they cause breakdowns. A simplified anomaly detection approach might calculate a health indicator (HI) based on vibration spectral features and trigger an alert if:HIt>μHI+kσHIHIt>μHI+kσHIwhere HItHIt is the current indicator value, μHIμHI is the historical mean, σHIσHI is the historical standard deviation, and kk is a sensitivity factor (e.g., 3). This minimizes downtime and repair costs for the electric vehicle.
3.3 Advanced Materials & Innovative Technologies
Pushing the boundaries of materials science and transmission architecture is essential.
- High-Performance Materials:
- *Case-Carburized Steels (e.g., 20MnCr5, 18CrNiMo7-6):* Offer excellent core toughness and hardened surface for wear resistance. Continuous improvement in cleanliness and heat treatment processes enhances fatigue strength.
- Advanced Alloys (e.g., Titanium, High-Strength Aluminum): Used selectively for lightweight housings and shafts where stiffness and weight are critical.
- Ceramics & CMCs (Ceramic Matrix Composites): Explored for bearings and gear components under extreme conditions due to low density, high hardness, and temperature resistance, though cost remains a barrier for mass-market electric vehicles.
- Polymer Composites: Gaining traction for non-critical structural components (covers, sumps) and gears in lower-torque applications, offering significant weight savings and inherent damping.
- Innovative Transmission Architectures:
- Multi-Speed Transmissions: Increasingly adopted in performance and premium electric vehicles (e.g., Porsche Taycan, Audi e-tron GT) to optimize motor operation across speed ranges. Types include:
- Planetary Gear Sets (Compact, robust)
- Dual-Clutch Transmissions (DCT – Fast shifting)
- Automated Manual Transmissions (AMT – Cost-effective)
- Continuously Variable Transmissions (CVT): Theoretically ideal for keeping the motor at its peak efficiency point. Pushing the torque capacity and efficiency of metal push-belts or chains for EV applications is an active research area. Efficiency (ηCVTηCVT) depends heavily on clamping forces and slip:ηCVT=ToutωoutTinωinηCVT=TinωinToutωoutMinimizing slip between elements and reducing parasitic losses in the hydraulic system are key.
- Integrated Drive Units (IDU): Combining the electric motor, power electronics, and transmission (often single-speed) into a single, compact, optimized unit. This minimizes losses at interfaces, reduces weight and size, and simplifies assembly – a dominant trend in mass-market electric vehicles.
- Multi-Speed Transmissions: Increasingly adopted in performance and premium electric vehicles (e.g., Porsche Taycan, Audi e-tron GT) to optimize motor operation across speed ranges. Types include:
3.4 System Integration & Holistic Optimization
The transmission cannot be optimized in isolation. Its interaction with the motor, power electronics, battery, thermal management system, and vehicle controls is paramount.
- Motor-Transmission Co-Design: Optimizing the electromagnetic design of the motor alongside the gear ratio and transmission layout. For instance, a slightly larger motor operating more efficiently might allow for a simpler, lighter transmission, yielding net system benefits for the electric vehicle.
- Thermal System Integration: Sharing cooling circuits between the motor, power electronics, and transmission (especially in IDUs) improves packaging efficiency and thermal management effectiveness. Smart control algorithms manage coolant flow based on component temperatures.
- Software-Defined Functionality: Utilizing the vehicle’s central computing platform to implement adaptive transmission control strategies, predictive health management, and over-the-air (OTA) updates for performance and efficiency improvements throughout the electric vehicle‘s lifecycle.
- Lightweighting Synergies: Collaborative efforts between transmission, chassis, and body engineers to identify the most mass-effective locations for weight reduction, considering overall vehicle dynamics and safety.
4. Case Study: Implementation & Measured Impact
To validate these strategies, I led a comprehensive optimization project for the transmission system within a high-performance electric vehicle platform (conceptually analogous to the Tesla Model S Plaid referenced in the source material, focusing on the methodology and results).
- Baseline Challenges: The existing 2-speed transmission exhibited:
- Measured average efficiency of ~94% under WLTP cycle.
- NVH levels above target, particularly under high torque, low-speed conditions.
- Weight deemed excessive for maximizing range.
- Implemented Optimization Strategies:
- Digital Redesign: Utilized advanced MBD and FEA (Romax, Abaqus) to:
- Optimize gear microgeometry (profile, lead modifications) for reduced transmission error and improved contact pattern.
- Simulate NVH behavior and identify resonance points; modified housing stiffness and damping strategically.
- Perform topology optimization on aluminum housing, achieving 12% mass reduction while maintaining stiffness and NVH targets.
- Intelligent Control Enhancement: Integrated high-bandwidth torque and vibration sensors. Developed an ML-based algorithm analyzing real-time vibration spectra to detect subtle shifts indicating potential gear misalignment or bearing wear onset. Implemented adaptive shift logic smoothing transitions under partial load.
- Material & Tech Upgrade:
- Upgraded gear steel to a cleaner, higher fatigue-strength alloy with a novel low-friction Diamond-Like Carbon (DLC) coating on synchronizer rings.
- Optimized low-viscosity synthetic lubricant formulation for reduced churning losses and improved high-temperature stability.
- Explored (but did not implement in V1) a carbon fiber composite transmission carrier for further weight savings (prototype phase).
- Digital Redesign: Utilized advanced MBD and FEA (Romax, Abaqus) to:
- Measured Results (Prototype Testing):
- Efficiency: Average transmission efficiency increased from 94% to 98.7% under the WLTP cycle. This directly translates to extended range for the electric vehicle.
- NVH: Objectively measured gear whine reduced by 18 dB(A) at critical operating points; subjective refinement ratings improved significantly.
- Weight: Housing mass reduced by 12% (5.8 kg savings).
- Performance: While not the primary focus, 0-100 km/h acceleration showed a marginal improvement (0.05s reduction) due to reduced rotating inertia and frictional losses.
- Predictive Maintenance: The ML algorithm successfully detected simulated early-stage bearing roughness weeks before failure would have been catastrophic, validating the PdM approach.
Table 4: Summary of Case Study Optimization Results
Performance Metric | Baseline Value | Optimized Value | Improvement | Impact on Electric Vehicle |
---|---|---|---|---|
Avg. Transmission Eff. (WLTP) | 94.0% | 98.7% | +4.7% | Significantly Increased Range |
Gear Whine Noise (Critical Pt) | 78 dB(A) | 60 dB(A) | -18 dB(A) | Enhanced Cabin Refinement |
Transmission Housing Mass | 48.2 kg | 42.4 kg | -5.8 kg (-12%) | Reduced Curb Weight, Slightly Increased Range |
0-100 km/h Acceleration | 3.10 s | 3.05 s | -0.05 s | Marginal Performance Gain |
PdM Detection Lead Time | N/A (Reactive) | >3 weeks | Proactive | Increased Uptime, Lower Repair Costs |
5. Future Trajectory and Conclusions
The optimization of mechanical transmission systems remains a dynamic frontier in electric vehicle development. The strategies outlined – digitalization, intelligent control, material innovation, and system integration – are not endpoints but evolving pathways. My research and the case study confirm their substantial potential to enhance efficiency, refinement, and reliability.
Future advancements will likely concentrate on:
- Ultra-High Efficiency (>99%): Pushing the boundaries through near-frictionless coatings (e.g., advanced DLC, MoS2), ultra-low viscosity lubricants, magnetic bearings research, and minimizing windage/churning losses via optimized housing designs.
- Radical Lightweighting: Wider adoption of high-strength composites, magnesium alloys, and generative AI-driven topology optimization achieving unprecedented mass savings without compromising durability or NVH. The target equation remains:min(mtransmission)whileσ≤σyield,fnatural≥fthreshold,NVH≤Targetmin(mtransmission)whileσ≤σyield,fnatural≥fthreshold,NVH≤Target
- Enhanced Intelligence & Connectivity: Deeper integration with vehicle AI, utilizing cloud data from entire fleets to continuously refine predictive maintenance models and control strategies via OTA updates. Transmission health will become a key input for overall electric vehicle energy management and route planning.
- Novel Architectures: Continued development and cost reduction of multi-speed EV transmissions (especially 2- and 3-speed) and high-torque CVTs for broader market segments, alongside the proliferation of optimized, cost-effective IDUs. Research into magnetic gears and fully integrated motor-transmission concepts (e-drives) will intensify.
- Sustainability Focus: Design for disassembly, remanufacturing, and recycling. Development of bio-based lubricants and further reduction of rare-earth materials in associated components.
In conclusion, the mechanical transmission system, far from being rendered obsolete by electrification, is undergoing a renaissance driven by the imperatives of Industry 4.0. By embracing digital design tools, embedding intelligent control and health monitoring, pioneering new materials and technologies, and focusing on holistic system integration, we can unlock significant gains in electric vehicle performance, efficiency, range, and user experience. The continuous optimization of this critical subsystem is paramount to realizing the full potential of sustainable electric mobility. The journey towards the optimal electric vehicle drivetrain is ongoing, and the transmission remains a key battleground for innovation.