The global shift toward sustainable transportation hinges on one critical component: the electric vehicle drive motor. As governments mandate phasing out internal combustion engines and consumers demand longer range and exhilarating performance, the sophistication of motor control systems becomes paramount. At the heart of this evolution lies vector control—a technology transforming humble induction motors into high-precision powerhouses capable of rivaling, and often surpassing, the responsiveness of traditional engines.
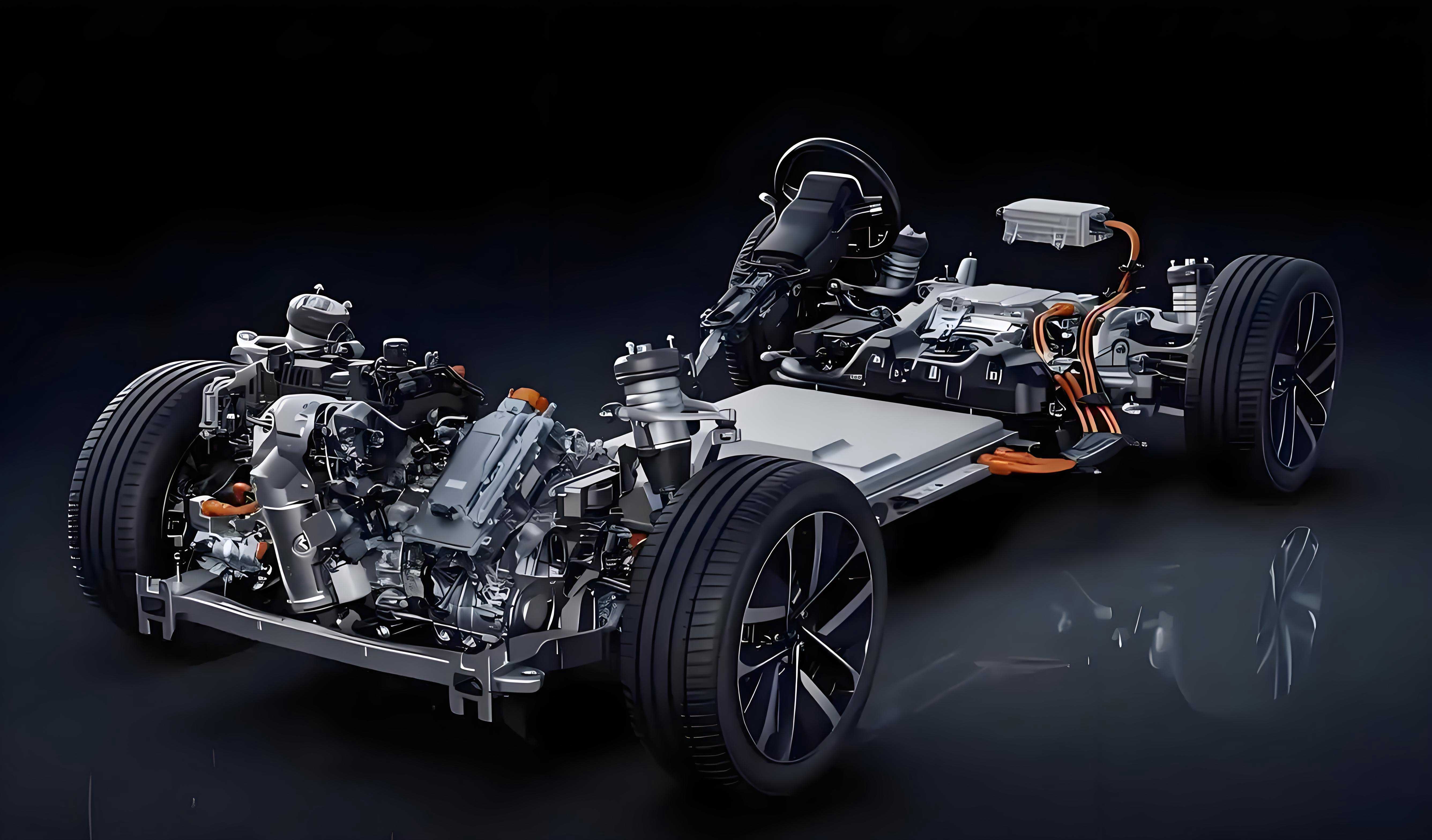
Why Electric Vehicles Demand Smarter Motor Control
Electric vehicles operate under uniquely demanding conditions. Unlike combustion engines, which generate torque through controlled explosions, electric motors must deliver instantaneous, seamless power across a vast speed range—from crawling in city traffic to high-speed cruising. This requires exquisite control over electromagnetic forces within the motor. Early methods, like basic variable-frequency drives, proved crude and inefficient, leading to jerky acceleration, wasted energy, and limited top speeds.
Vector control, formally known as Field-Oriented Control (FOC), emerged as the solution. By treating the alternating currents inside an AC motor like a precisely steerable “vector,” it mimics the independent control of torque and magnetic flux once exclusive to DC motors. The result? Smoother acceleration, higher efficiency, and the ability to extract maximum performance from every volt of the battery’s charge. For electric vehicle manufacturers, this translates directly into competitive advantage: extended range, superior drivability, and reduced component stress.
Decoding the Wizardry: How Vector Control Tames the AC Motor
The genius of vector control lies in its mathematical orchestration of three-phase AC currents. Here’s how it elevates electric vehicle performance:
- Coordinate Transformation: Seeing the Motor Differently
- Clarke Transform: Converts three-phase currents (a, b, c) into a two-axis stationary reference frame (α, β). This simplifies control by reducing variables.
- Park Transform: Further rotates the (α, β) frame into a synchronously rotating coordinate system (d, q). Crucially, the ‘d’ axis aligns with the rotor’s magnetic flux, while the ‘q’ axis governs torque generation. Now, engineers can directly manipulate the motor’s torque (via iq) and magnetic field strength (via id)—just like adjusting throttle and spark timing in an engine.
- Rotor Field Orientation: The Gold Standard
Early vector control experiments tested stator or air-gap magnetic alignment. Rotor field orientation emerged superior for electric vehicle applications due to its inherent simplicity and minimal coupling between torque and flux controls. By locking the control system’s ‘d’-axis to the rotor’s magnetic field:- Torque becomes directly proportional to the q-axis current (iq).
- Magnetic flux depends solely on the d-axis current (id).
This decoupling allows electric vehicles to achieve near-instantaneous torque adjustments—critical for regenerative braking responsiveness and dynamic stability control interventions.
- SVPWM: Maximizing Battery Voltage, Minimizing Waste
Traditional PWM techniques, like sinusoidal modulation (SPWM), waste precious battery voltage and generate excessive heat. Space Vector Pulse Width Modulation (SVPWM) revolutionizes this by treating the inverter and motor as a unified electromagnetic system. Instead of approximating a sine wave, SVPWM synthesizes a rotating voltage vector that traces a near-perfect circle. Benefits for electric vehicles are profound:- 15% higher DC-link voltage utilization → more torque at high speeds.
- Reduced harmonic losses → cooler operation and longer motor life.
- Smoother magnetic field rotation → near-silent motor operation.
Weak Magnetic Control: Unlocking Electric Vehicle Autobahn Performance
A critical limitation haunts electric vehicles at high speeds: as the motor spins faster, it generates a back-electromotive force (back-EMF) that opposes the battery voltage. Eventually, the inverter can’t push enough current to maintain torque—the motor “hits a wall.” Weak magnetic control smashes this barrier.
By deliberately reducing the magnetic field strength (flux) via the id current at elevated speeds, the back-EMF is suppressed. This allows the motor to safely enter a “constant power” region, extending its usable speed range by 30–50%. The implementation is elegantly simple:
i_d = \frac{i_{d,\text{rated}}}{\omega}
Where:
i_d
= d-axis (flux) currenti_{d,rated}
= rated flux current at base speedω
= rotor speed
While peak power decreases slightly in this zone, efficiency often increases due to lower core losses. For electric vehicle drivers, this means confident highway passing maneuvers and sustained high-speed cruising without battery-draining voltage limitations.
From Theory to Road: Validating the Electric Vehicle Advantage
Simulation and real-world testing validate vector control’s transformative impact. Using MATLAB/Simulink models replicating a 1500–3000 RPM induction motor drive:
- Torque Response: Near-instantaneous torque control with minimal overshoot (under 5%) even during step changes in demand.
- Speed Stability: Maintains target speed (e.g., 2200 RPM) within 0.2% error under no-load conditions, crucial for consistent regenerative braking energy capture.
- Weak Field Efficacy: Extends motor operation beyond base speed by 40% while maintaining over 92% system efficiency.
These aren’t laboratory curiosities. Major automakers like General Motors (EV1), Chrysler (EPIC), and Volkswagen (Golf EV) adopted induction motors with vector control precisely for their robustness, cost-effectiveness, and controllability—advantages that persist in next-generation electric vehicles.
The Road Ahead: Intelligent Control for Autonomous Electric Vehicles
Vector control’s precision lays the groundwork for future innovations. As electric vehicles evolve toward autonomous operation, motor control must integrate with broader vehicle dynamics systems:
- Torque Vectoring: Independently controlling motors on individual wheels for unprecedented cornering agility and stability.
- Predictive Energy Management: Anticipating terrain and traffic to optimize flux levels for minimum energy consumption.
- Fail-Operational Architectures: Redundant control algorithms ensuring motor reliability for SAE Level 4/5 autonomy.
Ongoing research focuses on “sensorless” vector control—eliminating costly position sensors by estimating rotor flux purely from motor current and voltage measurements. This promises further cost reductions and reliability gains for mass-market electric vehicles.
Conclusion: The Invisible Hand Guiding the EV Revolution
Vector control operates silently beneath the surface, unnoticed by drivers yet fundamental to the electric vehicle experience. By mastering the intricate dance of magnetic fields and currents, it delivers the smooth, relentless acceleration and uncanny efficiency defining modern EVs. As battery costs fall and energy density rises, the sophistication of motor control becomes the decisive battleground. Those mastering its nuances—rotor field orientation, SVPWM optimization, and adaptive weak magnetic strategies—will lead the charge toward an electric future where performance and sustainability are no longer trade-offs, but symbiotic realities. The electric vehicle isn’t just replacing the engine; it’s redefining motion itself, one precisely controlled magnetic pulse at a time.