As a researcher focusing on the aerodynamic performance of electric vehicles (EVs), I aim to address the critical challenge of enhancing driving range by optimizing vehicle shape. This study specifically investigates how adjusting the A-pillar inclination angle affects aerodynamic drag, a key factor influencing energy consumption in EVs. By leveraging computational tools and systematic simulations, I sought to validate the hypothesis that modifying the A-pillar geometry could significantly reduce wind resistance, thereby improving energy efficiency and extending driving range.
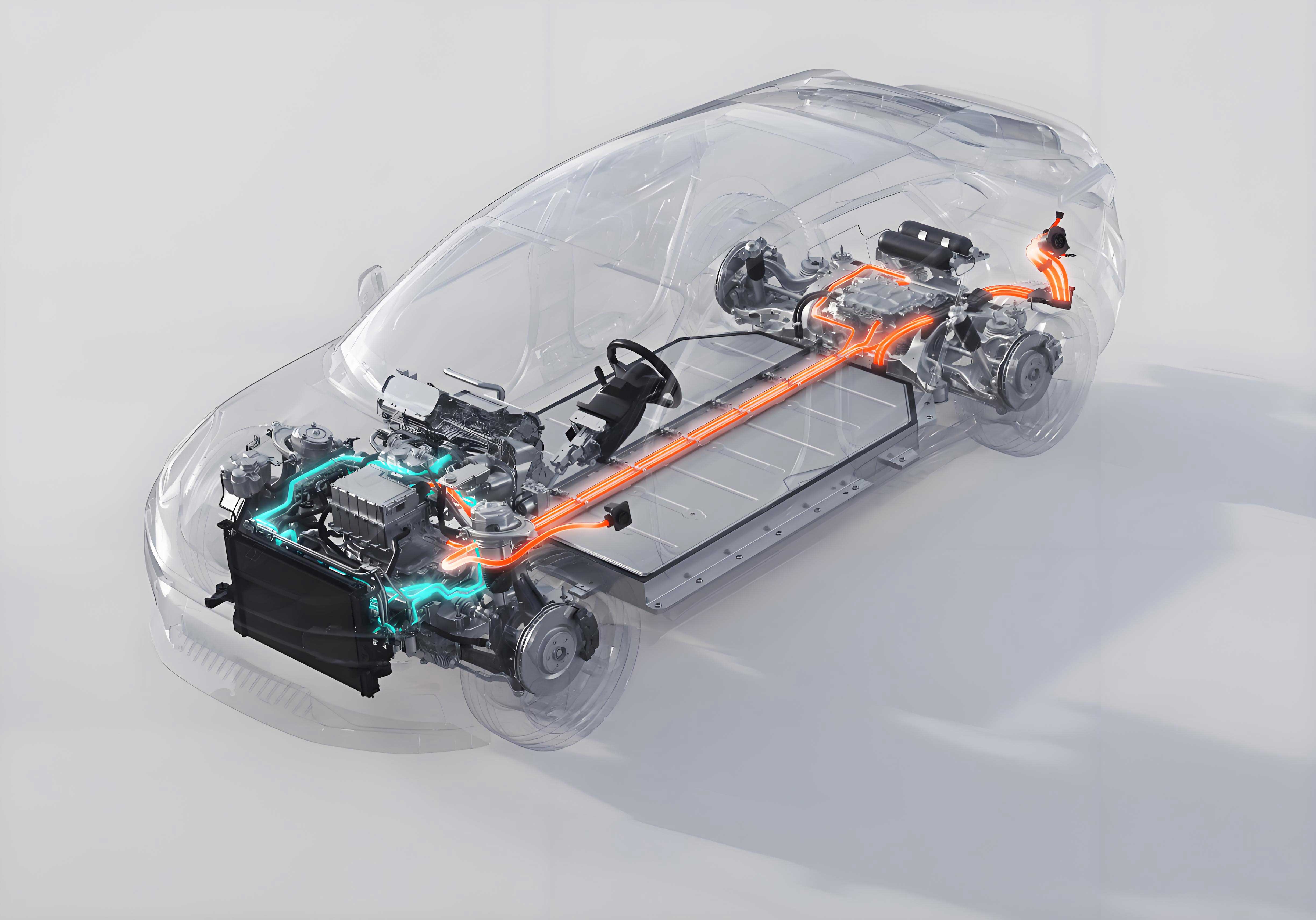
1. Introduction
The growing demand for electric vehicles has intensified research into improving their energy efficiency, with aerodynamic drag being a primary focus. In internal combustion engine vehicles, aerodynamic drag accounts for approximately 15–20% of total energy loss, but in EVs, this proportion can rise to 20–35% under NEDC driving conditions . Reducing aerodynamic drag is therefore crucial for maximizing battery efficiency and driving range.
The aerodynamic drag force (\(F_d\)) is described by the formula:\(F_d = \frac{1}{2} C_d \rho A v^2\) where:
- \(C_d\) = drag coefficient,
- \(\rho\) = air density,
- A = front-facing area of the vehicle,
- v = driving speed .
This equation highlights two primary targets for reduction: \(C_d\) (drag coefficient) and A (frontal area). Among vehicle design elements, the A-pillar inclination angle—a key component of the front-end geometry—plays a significant role in airflow separation and pressure distribution. Previous studies have shown that optimizing the A-pillar angle can reduce airflow separation at the front, thereby lowering \(C_d\) .
2. Methodology
2.1 Model Development
2.1.1 Initial Model Setup
I selected the Tesla Model S as the baseline for the initial model due to its established aerodynamic design and publicly available dimensions. Using CATIA and SolidWorks, I created a 3D model focusing on the front windshield and hood transition area, which is critical for aerodynamic performance. The original model dimensions were \(4921.182 \, \text{mm (length)} \times 1920 \, \text{mm (width)} \times 1268.584 \, \text{mm (height)}\) .
2.1.2 Optimization of A-Pillar Inclination
To systematically analyze the impact of A-pillar angle on drag, I designed three models with different inclination angles:
- Original model: \(162.765^\circ\),
- Model 2: \(161.786^\circ\),
- Model 3: \(165^\circ\).
The optimization process involved:
- Projecting the baseline model onto the YZ plane to isolate the A-pillar and hood transition region.
- Adjusting geometric parameters (height and width) via parametric sketching in SolidWorks to maintain design continuity.
- Ensuring the frontal width (\(1920 \, \text{mm}\)) remained constant across all models for comparative accuracy .
Table 1 summarizes the A-pillar angles for each model:
Table 1. A-Pillar Inclination Angles Across Models
Model | A-Pillar Inclination Angle |
---|---|
Original | \(162.765^\circ\) |
Model 2 | \(161.786^\circ\) |
Model 3 | \(165^\circ\) |
2.2 Computational Fluid Dynamics (CFD) Simulation
2.2.1 Simulation Setup with STAR-CCM+
I used STAR-CCM+ to perform CFD analyses, focusing on:
- Computational Domain: Extended to \(3 \times \text{vehicle length}\) upstream, \(7 \times \text{vehicle length}\) downstream, \(7 \times \text{vehicle width}\) laterally, and \(5 \times \text{vehicle height}\) vertically to mimic real-world airflow .
- Grid Generation: Approximately 5 million tetrahedral cells with two-layer full \(y^+\) wall treatment to resolve boundary layer effects.
- Turbulence Model: k-ε model with Reynolds-Averaged Navier-Stokes (RANS) equations for steady-state flow simulation.
- Boundary Conditions: Inlet velocity set to \(30 \, \text{m/s}\) (approx. \(108 \, \text{km/h}\)), corresponding to typical highway driving speeds .
2.2.2 Key Metrics
The primary output was the drag coefficient (\(C_d\)), calculated using:\(C_d = \frac{2F_D}{\rho A v^2}\) where \(F_D\) is the frontal drag force obtained from simulation results.
3. Results
3.1 Baseline Simulation (Original Model)
The original Tesla Model S–based model yielded a \(C_d\) of \(0.501\) at \(30 \, \text{m/s}\). Pressure distribution analysis revealed high positive pressure at the front bumper and abrupt airflow separation at the A-pillar, contributing to increased drag .
3.2 Optimized Models
3.2.1 Model 2 (\(161.786^\circ\))
Reducing the A-pillar angle (steeper inclination) slightly increased the frontal area but improved airflow smoothness. The simulated \(C_d\) dropped to \(0.427\), a \(14.8\%\) reduction from the original model .
3.2.2 Model 3 (\(165^\circ\))
Increasing the A-pillar angle (shallower inclination) significantly reduced airflow separation. The \(C_d\) decreased to \(0.325\), a \(35.1\%\) reduction from the original model—the most substantial improvement among the three designs .
Table 2 summarizes the drag coefficient changes:
Table 2. Drag Coefficient (\(C_d\)) Comparison
Model | A-Pillar Angle | \(C_d\) | Percentage Reduction from Original |
---|---|---|---|
Original | \(162.765^\circ\) | \(0.501\) | — |
Model 2 | \(161.786^\circ\) | \(0.427\) | \(14.8\%\) |
Model 3 | \(165^\circ\) | \(0.325\) | \(35.1\%\) |
3.3 Pressure Distribution Analysis
Pressure cloud maps showed that:
- The original model had a concentrated high-pressure zone at the front windshield-A-pillar junction.
- Model 3 exhibited a more uniform pressure gradient across the front surface, with reduced maximum pressure on the windshield. This indicated smoother airflow and less turbulent separation .
4. Discussion
4.1 Mechanisms of Drag Reduction
The A-pillar inclination affects drag through two primary mechanisms:
- Airflow Separation: A shallower angle (Model 3) delays airflow separation at the A-pillar, reducing wake turbulence and drag.
- Pressure Distribution: Optimized geometry reduces frontal pressure buildup, as seen in the more uniform pressure cloud maps for Model 3 .
4.2 Implications for EV Range
Based on literature, a \(0.1\) reduction in \(C_d\) can decrease high-speed energy consumption by approximately \(20\%\) and extend driving range by \(7 \, \text{km}\) . For Model 3, the \(0.176\) reduction in \(C_d\) suggests a potential range increase of \(12.3 \, \text{km}\) at highway speeds, demonstrating the practical significance of aerodynamic optimization for EVs.
4.3 Design Trade-offs
While Model 3 showed the best aerodynamic performance, real-world implementation must consider:
- Visibility: Extremely shallow A-pillar angles could compromise driver visibility.
- Manufacturing Complexity: Smooth transitions may require advanced manufacturing techniques.
- Component Integration: Compatibility with side mirrors and window designs .
5. Conclusion
This study demonstrates that optimizing the A-pillar inclination angle is an effective strategy to reduce aerodynamic drag in electric vehicles. Through CFD simulations and parametric modeling, I validated that increasing the A-pillar angle to \(165^\circ\) (Model 3) significantly reduces \(C_d\) by (35.1%), enhancing energy efficiency and driving range. These findings highlight the importance of front-end geometry in EV design and provide a foundation for future multi-parameter optimizations, such as integrating A-pillar design with rear diffusers and underbody streamlining.
For the EV industry, these results offer a practical roadmap to balance aesthetic design with aerodynamic performance, ultimately contributing to more sustainable and efficient electric mobility.