As a researcher in the automotive industry, I have closely observed the rapid evolution of electric vehicles (EVs) as they strive to address two critical challenges: limited driving range and lengthy charging times. These issues, often referred to as “range anxiety” and “charging anxiety,” have been major bottlenecks hindering the widespread adoption of EVs. To overcome these hurdles, automakers worldwide have turned to high-voltage platforms, with the 800V system emerging as a leading solution. This article delves into the development, advantages, technical challenges, and future prospects of the 800V high voltage platform in electric vehicles, emphasizing its role in transforming the EV landscape.
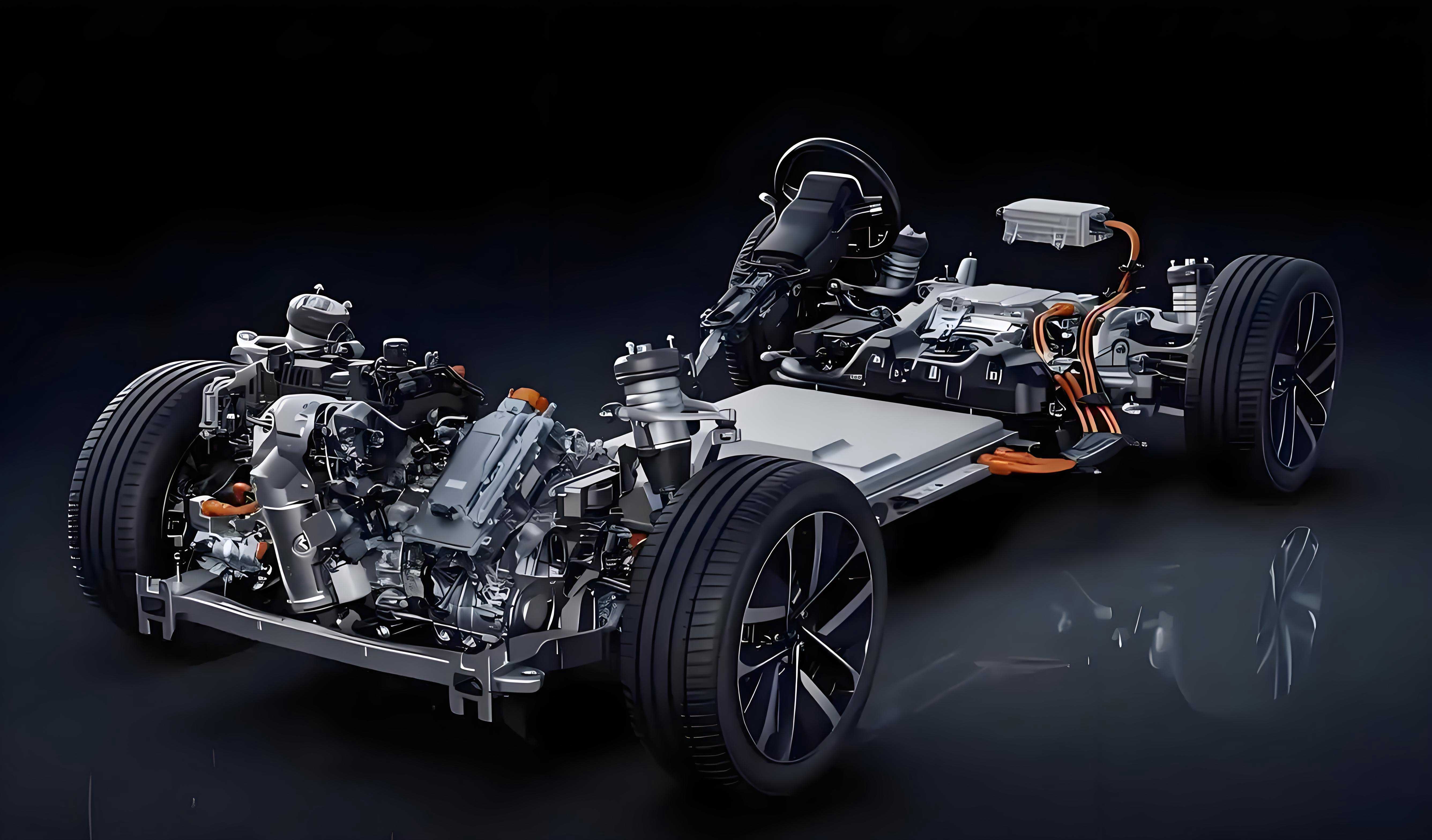
1. The Imperative for High Voltage in Electric Vehicles
Electric vehicles are celebrated for their potential to mitigate energy crises and environmental degradation. However, their market penetration has been constrained by consumer concerns over 续航里程 (driving range) and charging efficiency. Traditional 400V platforms, while prevalent, face inherent limitations in achieving rapid charging without compromising safety and performance.
1.1 The Power Equation: Voltage vs. Current
The fundamental principle governing charging speed is derived from the power formula:\(P = U \times I\) where P is power (in watts), U is voltage (in volts), and I is current (in amperes). To increase charging power P, one must either raise U or I. Early attempts to enhance charging speed focused on high-current solutions, as seen in the Tesla Model 3, which achieves fast charging at 400V by delivering high currents. However, this approach introduces significant challenges:
- Joule Heating: According to \(Q = I^2 R t\), where Q is heat generated, doubling the current quadruples heat production, leading to increased energy loss and reduced range .
- Weight and Cost: Thicker wires are required to handle high currents, increasing vehicle weight and manufacturing costs .
- Thermal Management: Enhanced cooling systems are necessary, adding complexity and further costs .
In contrast, increasing voltage (e.g., to 800V) reduces the required current for the same power, alleviating these issues. For example, a 350kW charger at 400V requires 875A, whereas at 800V, the current drops to 437.5A—halving heat generation and enabling thinner, lighter wiring .
2. Global Adoption of the 800V Platform
The shift toward 800V platforms has gained momentum since Porsche introduced the Taycan, the first production EV with an 800V architecture, in 2019. Below is a comparative overview of key automakers and their 800V initiatives:
Automaker | Model | Voltage (V) | Charging Power (kW) | Charging Speed (km in X min) | Launch Year | Key Features |
---|---|---|---|---|---|---|
Porsche | Taycan | 800 | 270 | 100 km in 4 min | 2019 | First 量产 800V 车型,800V-only architecture |
BAIC BluePark | ARCFOX αS HI | 800+ | 187 | 197 km in 10 min | 2021 | Partnered with Huawei for high-voltage tech |
GAC Aion | AION V Plus | 880 | 480 | 200 km in 5 min | 2021 | Graphene 6C battery, 880V supercharger |
BYD | e 3.0 Platform | 800 | N/A | 150 km in 5 min | 2021 | Built-in 800V supercharging technology |
Xiaopeng | G9 | 800 | 480 | 200 km in 5 min (10-80% in 15 min) | 2021 | SiC platform, extensive supercharger network |
Ideal Auto | MEGA | 800+ | 500+ | 500 km in 10 min | 2023 | Partnered with CATL for 5C battery cells |
This table highlights the diversity of approaches, from pure 800V architectures (Porsche) to hybrid systems using DC/DC converters (BYD). Notably, automakers are not only upgrading vehicles but also investing in proprietary charging infrastructure, such as Xiaopeng’s S4 superchargers, which reach 480kW and cover major cities in China .
3. Technical Advantages of 800V Platforms
The transition to 800V offers several technical benefits that address the limitations of traditional 400V systems:
3.1 Enhanced Charging Efficiency
By reducing current, 800V platforms enable faster charging with minimal energy loss. For instance, the Porsche Taycan can recharge from 5% to 80% in 22.5 minutes using a 270kW charger, while maintaining a relatively low current of ~337A . This contrasts with the Tesla Model 3’s high-current approach, which requires careful battery state management (e.g., charging only at 10-30% SOC for maximum power) .
3.2 Reduced Weight and Cost
Lower current in 800V systems allows for smaller-diameter copper wires. For example, a 400V system carrying 500A might require a 50mm² wire, whereas an 800V system with 250A can use a 16mm² wire—reducing weight by ~68% and cost by ~50% . Additionally, smaller connectors and simplified thermal management further optimize vehicle design.
3.3 Scalability for Higher Power
As charging power targets rise (e.g., 600kW+), 800V becomes indispensable. At 1000V, a 600kW charger would require only 600A, whereas a 400V system would need 1500A—an impractical current for safe, sustained operation. Thus, 800V serves as a foundational step toward future ultra-high-power charging .
4. Challenges in 800V Platform Implementation
Despite its promise, the 800V platform faces significant technical and logistical hurdles that require collaborative solutions across the industry.
4.1 Standardization of Safety and Charging Protocols
Current EV charging standards, such as China’s GB/T 18487 series, are tailored for 400V systems. Upgrading to 800V necessitates revised safety protocols for:
- Insulation and Arc Protection: Higher voltages increase the risk of electrical arcs and insulation failure, requiring robust materials and design .
- Interoperability: Proprietary charging systems (e.g., Tesla Superchargers, Xiaopeng’s S4 network) limit cross-brand compatibility, necessitating unified standards for connectors, communication protocols, and power management .
In 2024, China’s Ministry of Industry and Information Technology began drafting new national standards for 800V charging safety, focusing on fault detection, emergency shutdown mechanisms, and electromagnetic compatibility .
4.2 Vehicle Architecture Redesign
Two primary 800V architectures have emerged, each with distinct challenges:
- Pure 800V Architecture (e.g., Porsche Taycan):
- Requires all high-voltage components (e.g., motors, inverters, OBCs) to support 800V, increasing component costs due to low initial production volumes .
- Relies entirely on 800V charging infrastructure, which is currently scarce .
- Dual-Voltage Architecture (e.g., BYD e 3.0):
- Uses a DC/DC converter to step up 400V power to 800V for charging, allowing compatibility with existing 400V components and chargers .
- Introduces additional weight and complexity due to the DC/DC converter, potentially offsetting some efficiency gains .
The table below compares these architectures:
Architecture Type | Advantages | Disadvantages | Component Compatibility | Charging Flexibility |
---|---|---|---|---|
Pure 800V | Simplified design, higher efficiency | High component costs, limited infrastructure | 800V-only components | Requires 800V chargers |
Dual-Voltage (400V/800V) | Uses existing 400V parts, 兼容 old chargers | Added weight (DC/DC converter), lower efficiency | 400V and 800V components | Works with 400V and 800V chargers |
4.3 High-Voltage Wiring and Thermal Management
While standard high-voltage cables can handle 800V, fast-charging cables face severe thermal stress. For example, a 480kW charger at 800V draws 600A, generating significant heat in the charging gun and cable. Liquid-cooled cables, which circulate coolant through internal channels, have emerged as a solution, but they are bulky and lack standardized safety guidelines .
4.4 Charging Infrastructure Gap
As of 2025, fewer than 10% of public chargers globally support 800V, with most concentrated in urban areas. Automakers like Xiaopeng have deployed over 233 S4 superchargers in China, but inter-brand compatibility remains an issue . Standardizing charger design and protocols is critical to avoiding a fragmented network, akin to the early days of EV charging when competing standards (e.g., CHAdeMO, CCS) caused confusion.
5. Future Outlook and Industry Implications
The 800V platform is more than a technical upgrade; it represents a paradigm shift in how we design, charge, and integrate electric vehicles into daily life. Here are key trends shaping its future:
5.1 Material and Component Innovations
- Silicon Carbide (SiC) Inverters: SiC devices offer lower switching losses and higher temperature tolerance than traditional silicon, making them ideal for 800V systems. Brands like Xiaopeng and Porsche have already adopted SiC inverters to improve efficiency .
- Solid-State Batteries: Emerging solid-state batteries could withstand higher voltages and faster charging, potentially enabling 10-minute full charges by 2030 .
5.2 Infrastructure Development
To support 800V adoption, governments and industry players must invest in:
- Grid Upgrades: High-power chargers (350kW+) require robust grid connections, necessitating upgrades to transmission and distribution networks.
- Public-Private Partnerships: Models like the EU’s “Alternative Fuels Infrastructure Regulation,” which mandates high-power chargers along major highways, can accelerate deployment.
5.3 Safety and Sustainability
As voltages rise, emphasis on recyclability and eco-friendly materials will grow. For example, using aluminum instead of copper in wiring could reduce weight and environmental impact, though challenges in conductivity remain.
6. Conclusion
From my perspective, the 800V high voltage platform is a pivotal innovation that addresses the core limitations of electric vehicles. By prioritizing voltage over current, automakers can achieve faster charging, lighter designs, and improved efficiency—all while reducing operational costs. However, its success hinges on overcoming standardization barriers, scaling infrastructure, and fostering cross-industry collaboration.
As the industry transitions toward 800V and beyond, electric vehicles will not only match but surpass the convenience of internal combustion engine cars. The journey ahead requires technical prowess, strategic policy support, and a unified vision for a sustainable automotive future. The 800V platform is not just a step forward; it is a leap into a new era of electric mobility.