Abstract
As the popularity of electric vehicles (EVs) continues to rise, electric vehicle charging piles have become a critical component of the charging infrastructure. This study focuses on improving the measurement accuracy and energy efficiency evaluation of these charging piles. By analyzing the shortcomings of existing metering technologies, we propose hardware optimization, algorithm improvement, and digital calibration schemes. Additionally, we establish an energy efficiency evaluation index system and a dynamic evaluation model. Experimental results show that optimizing sensor design, introducing Kalman filtering and harmonic compensation algorithms, and implementing a multi-point calibration strategy can significantly enhance measurement accuracy to ±0.2% and achieve energy efficiency evaluation accuracy within ±2%. These findings provide technical support for performance optimization and energy-saving retrofits of charging piles.
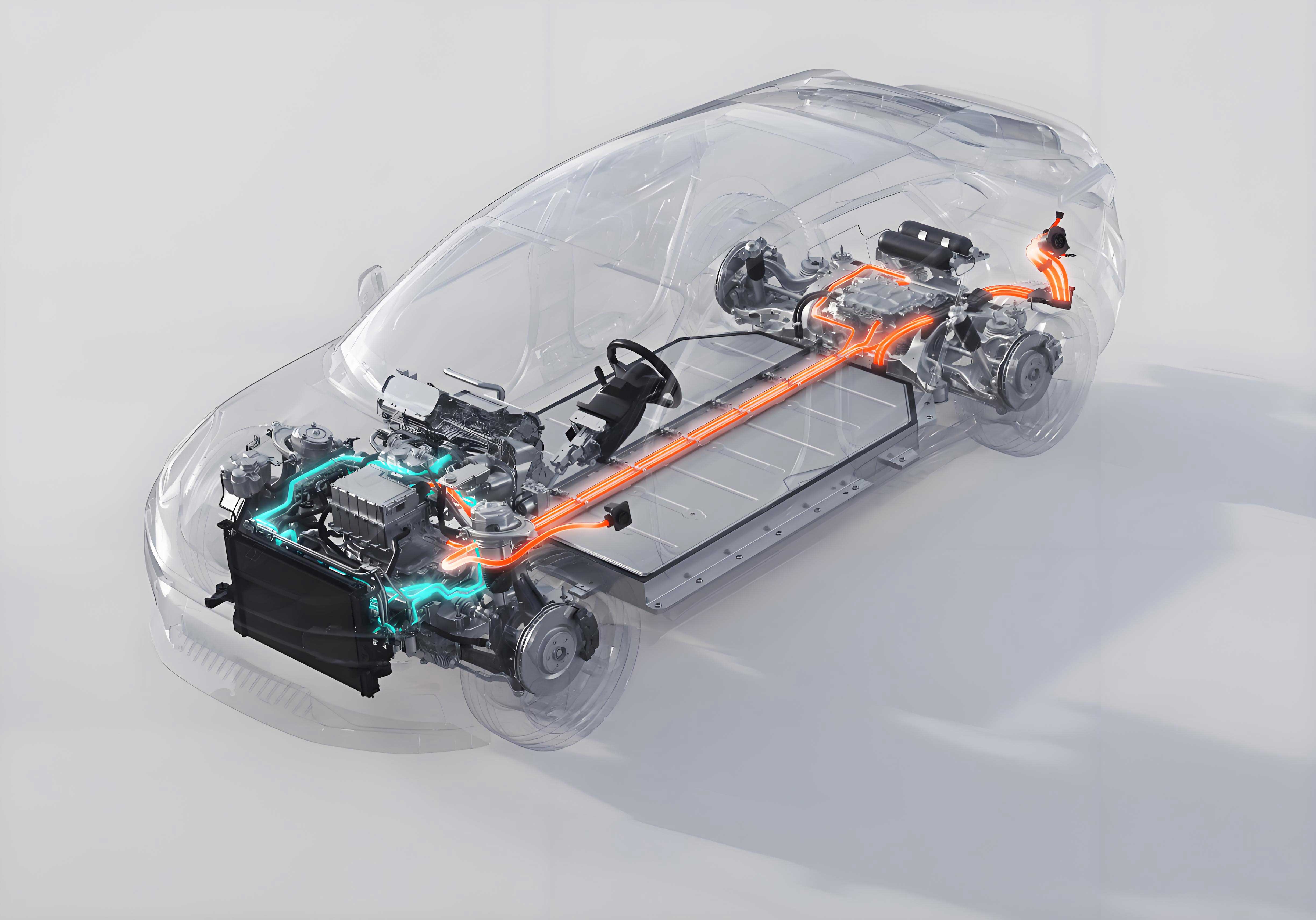
Keywords:
Electric vehicle; Charging pile; Measurement accuracy; Energy efficiency evaluation; Calibration
1. Introduction
The rapid development of electric vehicles has driven the expansion of charging infrastructure. Charging piles, as the core devices for energy transfer, play a pivotal role in ensuring user experience and energy utilization efficiency. However, current metering technologies for charging piles face challenges such as temperature drift, external interference, and low precision in low-current segments. Moreover, energy efficiency evaluation methods lack unified standards, hindering the standardized development of the industry. This research aims to address these issues by proposing systematic solutions to improve measurement accuracy and establish a scientific energy efficiency evaluation framework for electric vehicle charging piles.
2. Methods for Improving Measurement Accuracy
2.1 Hardware-Level Precision Enhancement
To tackle temperature drift and external interference, we focus on optimizing sensor selection and signal conditioning circuits.
2.1.1 Sensor Design
- Dual Hall Differential Structure: We employ two Hall elements arranged in reverse to cancel out common-mode interference and temperature drift. A magnetic shielding layer is added to reduce external magnetic field interference, enhancing sensor stability .
- Performance Metrics: The optimized sensor achieves a signal-to-noise ratio (SNR) > 85 dB, gain error < 0.02%, linearity < 0.01%, temperature drift coefficient < 100 ppm/°C, and common-mode rejection ratio (CMRR) > 100 dB .
2.1.2 Signal Conditioning Circuit
- Operational Amplifier: The low-temperature drift operational amplifier AD8554 (temperature drift coefficient < 1 μV/°C) is used, along with a temperature-compensated reference voltage source .
- Dual-Range Circuit: A switchable gain structure is designed to automatically switch to a high-gain channel when the load current is below 20% of the rated value, ensuring accuracy in low-current segments .
2.1.3 Analog-to-Digital Conversion (ADC)
- The 16-bit SAR-type ADC chip ADS8885 is adopted, supporting differential input and offering high precision and strong anti-interference capabilities .
Table 1: Hardware Optimization Summary
Component | Optimization Measure | Key Performance 指标 |
---|---|---|
Sensor | Dual Hall differential structure with magnetic shielding | SNR > 85 dB, CMRR > 100 dB |
Signal Conditioning | Low-temperature drift op-amp (AD8554), dual-range circuit | Temperature drift < 1 μV/°C |
ADC | 16-bit SAR-type ADC (ADS8885) | Resolution: 16 bits |
2.2 Algorithm-Level Precision Enhancement
Three modules are developed: digital filtering, harmonic compensation, and adaptive calibration.
2.2.1 Digital Filtering: Improved Kalman Filter
- A state-space model of the current signal is established to separate the signal from noise. Filter parameters are dynamically adjusted based on the current’s dynamic characteristics to avoid weakening dynamic signals .
- Mathematical Model:\(I(t) = I_0(t) + \sum_{n=1}^{N} A_n \sin(n\omega t + \phi_n)\) where \(I_0(t)\) is the fundamental component, and \(A_n\) and \(\phi_n\) are the amplitude and phase of the nth harmonic .
2.2.2 Harmonic Compensation
- Based on fast Fourier transform (FFT) analysis, the amplitude and phase of major harmonics are extracted to compensate for their effects using the following model:\(I_{\text{compensated}} = I_{\text{measured}} – \sum_{n=2}^{N} A_n \sin(n\omega t + \phi_n)\) This restores the authenticity of the fundamental wave signal .
2.2.3 Adaptive Calibration
- Real-time monitoring of environmental parameters (e.g., temperature, humidity) is used to dynamically adjust the gain coefficient and zero offset of the measurement system, reducing errors caused by environmental changes .
2.3 Digital Calibration Scheme
A multi-point, multi-condition calibration strategy is adopted, covering the full temperature and range.
2.3.1 Factory Calibration
- Conducted in a constant-temperature environment, data are collected at 5%, 20%, 50%, 80%, and 100% load points using a high-precision power analyzer. A reference calibration curve is fitted via least-squares method .
2.3.2 Online Calibration
- Utilizes built-in temperature sensors and current detection circuits to collect real-time operating parameters. Pre-set calibration data are used to dynamically adjust measurement error compensation .
- Calibration data are stored in FLASH to ensure integrity during power outages and facilitate continuous optimization .
3. Energy Efficiency Evaluation Method for Charging Piles
3.1 Energy Efficiency Evaluation Index System
The index system is constructed based on an “input-output-loss” framework, covering three levels: charging efficiency, conversion efficiency, and system total efficiency .
Table 2: Energy Efficiency Evaluation Index System
Evaluation Dimension | Specific Index | Calculation Method |
---|---|---|
Charging Efficiency | Charging Efficiency (\(\eta_1\)) | \(\eta_1 = \frac{\text{Output Energy}}{\text{Input Energy}} \times 100\%\) |
Power Factor (PF) | \(PF = \frac{\text{Active Power}}{\text{Apparent Power}}\) | |
Total Harmonic Distortion (THD) | \(THD = \frac{\sqrt{\sum_{n=2}^{\infty} A_n^2}}{A_1} \times 100\%\) | |
Conversion Efficiency | Conversion Efficiency (\(\eta_2\)) | \(\eta_2 = \frac{\text{Output Power of Conversion Unit}}{\text{Input Power of Conversion Unit}} \times 100\%\) |
Peak Efficiency (\(\eta_{\text{peak}}\)) | Maximum efficiency at rated load | |
System Efficiency | Weighted Efficiency (\(\eta_{\text{weighted}}\)) | Averaged efficiency across different load ratios |
3.2 Evaluation Model
A hierarchical modeling approach is used, covering power electronic conversion units, control units, and auxiliary systems.
3.2.1 Power Device Loss Model (IGBT/MOSFET)
- Switching Loss:\(P_{\text{switching total}} = (E_{\text{on}} + E_{\text{off}}) \times f\) where \(E_{\text{on}}\) and \(E_{\text{off}}\) are turn-on and turn-off energies, and f is the switching frequency .
- Conduction Loss:\(P_{\text{conduction}} = V_{\text{CE}} \times I_{\text{C}}\) where \(V_{\text{CE}}\) is the collector-emitter voltage, and \(I_{\text{C}}\) is the collector current .
3.2.2 System Total Loss Model\(P_{\text{total loss}} = P_{\text{conversion loss}} + P_{\text{control loss}} + P_{\text{auxiliary loss}}\)
- \(P_{\text{control loss}}\): Power consumption of DSP/MCU, driver circuits, and sampling circuits (obtained via lookup tables) .
- \(P_{\text{auxiliary loss}}\): Power consumption of fans, displays, etc. (obtained via lookup tables) .
3.2.3 Dynamic Evaluation Model Considering temperature (T) and load rate (L):\(\eta_{\text{system}}(T, L) = \eta_0 \times \left[1 – \alpha(T – T_0)\right] \times \left[1 – \beta(1 – L)\right]\) where:
- \(\eta_0\): Efficiency under standard conditions,
- \(T_0\): Reference temperature,
- \(\alpha\): Temperature coefficient,
- \(\beta\): Load coefficient .
4. Experimental Validation and Analysis
4.1 Experimental Setup
- Test Platform: A prototype charging pile with dual Hall sensors, rated power 60 kW, output voltage 200–750 V, maximum current 200 A .
- Measurement Accuracy Test: Conducted at -20°C, 25°C, and 50°C, with load ratios of 10%, 20%, 40%, 60%, 80%, and 100%. Data were collected every 1 second for 30 minutes per condition .
- Energy Efficiency Evaluation: Tested at 25°C with load ratios from 10% to 100%, recording data after 15 minutes of stabilization at each point .
4.2 Results
4.2.1 Measurement Accuracy
- After optimization, the measurement accuracy reached ±0.2% across all temperature and load ranges, significantly improving over traditional methods .
4.2.2 Energy Efficiency Test Results Table 3: Energy Efficiency Test Data at 25°C
Load Rate (%) | Conversion Efficiency (%) | Charging Efficiency (%) | System Efficiency (%) | Power Factor | THD (%) |
---|---|---|---|---|---|
10 | 88.5 | 90.2 | 87.8 | 0.92 | 3.5 |
30 | 92.3 | 93.5 | 91.8 | 0.95 | 2.8 |
50 | 95.1 | 95.8 | 94.5 | 0.98 | 2.2 |
80 | 96.0 | 96.5 | 95.2 | 0.99 | 1.8 |
100 | 95.5 | 96.0 | 94.8 | 0.99 | 1.5 |
- Key Observations:
- Energy efficiency exhibits a non-linear relationship with load rate, peaking at 80% load .
- A 10°C increase in temperature leads to an average 0.5% decrease in system efficiency due to changes in power device switching characteristics .
5. Conclusion
This study presents comprehensive solutions to enhance the measurement accuracy and energy efficiency evaluation of electric vehicle charging piles. Through hardware optimization (dual Hall sensors, low-temperature drift circuits), algorithm improvements (Kalman filtering, harmonic compensation), and a digital multi-point calibration strategy, measurement accuracy is elevated to ±0.2%. The established energy efficiency evaluation index system and dynamic model achieve an evaluation accuracy of ±2%, providing a scientific basis for performance optimization.
Future research should focus on refining precision calibration techniques under dynamic environmental conditions and expanding the applicability of energy efficiency evaluation models to complex scenarios, such as varying climatic conditions and diverse EV charging profiles. This will further solidify the technical foundation for the sustainable development of electric vehicle charging infrastructure.