As a metrology technician specializing in electric vehicle (EV) charging infrastructure, I have dedicated significant time to understanding the complexities of charging pile verification. The rapid expansion of EVs globally, particularly in China, has necessitated rigorous standards for these critical energy delivery systems. This article explores the technical hurdles, regulatory frameworks, and future directions in EV charging pile verification, emphasizing the importance of accurate metrology in safeguarding consumer trust and promoting sustainable mobility.
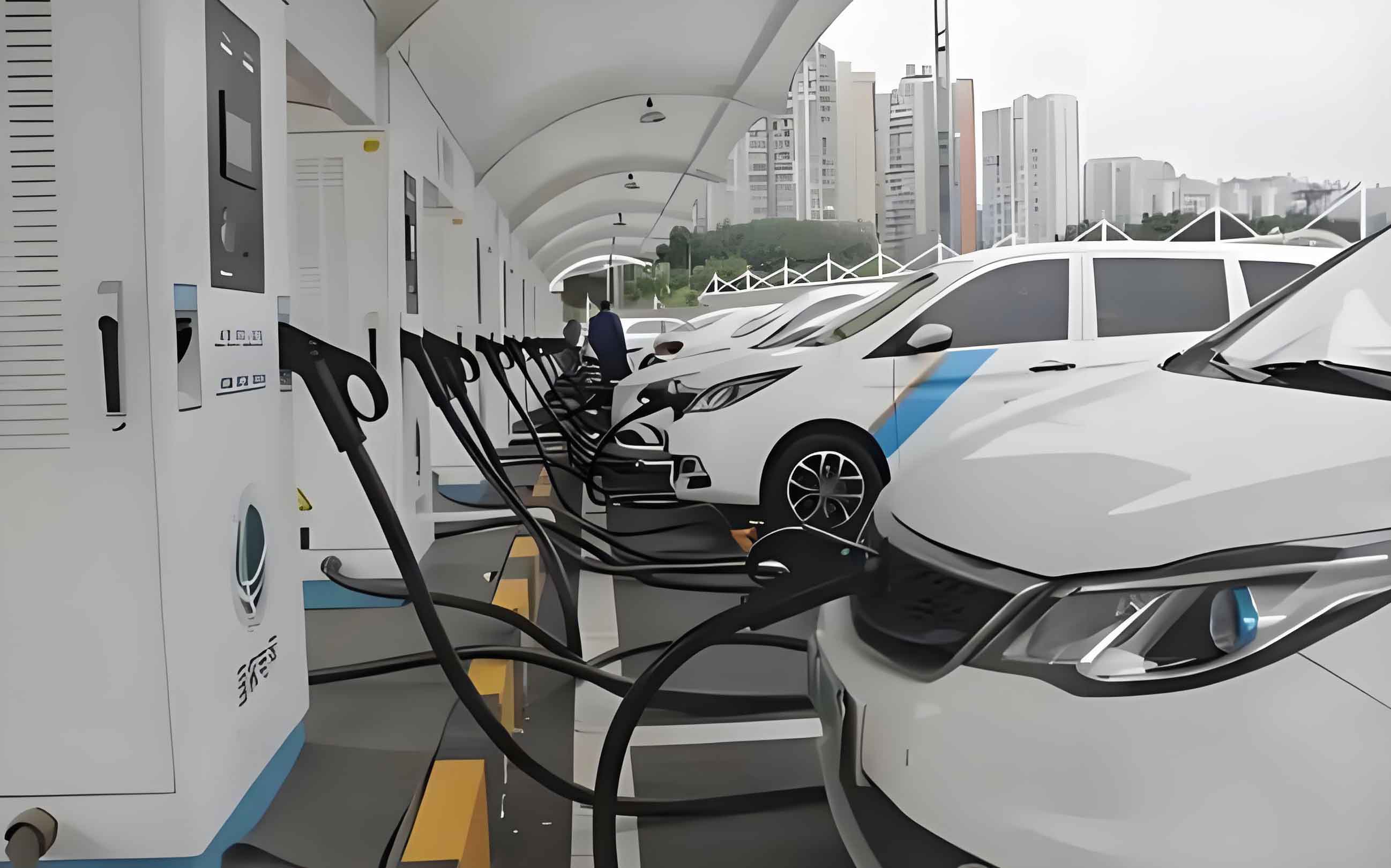
1. The Landscape of EV Charging Pile Verification
1.1 Policy and Regulatory Foundations
China’s commitment to low-carbon transportation is evident in its New Energy Vehicle Industry Development Plan (2021–2035), which mandates that EVs account for 20% of new vehicle sales by 2025 . Concurrently, the Market Regulation Administration’s Announcement No. 42 of 2020 classifies all trade-settlement charging piles as compulsory verification instruments, effective January 1, 2023 . This legal framework underscores the need for precise energy measurement to protect consumers from billing discrepancies.
At my institution, the Chifeng Product Quality Inspection and Testing Center, we obtained accreditation for EV charging pile verification in July 2023. Using specialized equipment like the EV AC Charging Pile Verification Device and Non-Vehicle Charger Verification Device, we conduct mandatory checks aligned with national standards .
1.2 Technical Classification of Charging Piles
EV charging piles are broadly categorized into two types, each with distinct operational mechanics:
Type | Energy Conversion | Charging Speed | Typical Installation Sites |
---|---|---|---|
DC Charging Piles | AC to DC via rectification | High (fast charging) | Highways, urban hubs |
AC Charging Piles | Direct AC supply | Low (slow charging) | Residential areas, public parking lots |
DC piles dominate high-traffic zones due to their ability to recharge vehicles in minutes, while AC piles are preferred for overnight charging in homes . Both types rely on integrated metrology modules to track energy consumption, which must be verified against national standards .
1.3 Current Verification Methodology
The core verification process involves serial connection of the charging pile, load bank, and standard meter (Figure 1). Key 检定项目 (verification items) include:
- Visual and Functional Inspection: Ensuring physical integrity and operational buttons work.
- Working Error Test: Comparing the pile’s energy display with the standard meter.
- Clock Error Test: Calibrating timekeeping accuracy for billing consistency .
The error calculation formula is:\(\text{Error (\%)} = \frac{\text{Charging Pile Reading} – \text{Standard Meter Reading}}{\text{Standard Meter Reading}} \times 100\%\) A pile is deemed compliant if errors fall within ±0.5% for DC piles and ±1.0% for AC piles, as specified in JJG 1148–2022 and JJG 1149–2022 .
2. Persistent Challenges in Field Verification
Over 2000 charging piles are installed across Chifeng, but our team faces three recurring obstacles during on-site inspections:
2.1 Mechanical Design and Installation Flaws
Many piles are poorly designed for metrology access:
- Inaccessible Sealing Points: 30% of inspected piles lack designated areas for security seals on metrology modules .
- Ambiguous Internal Layouts: In 25% of cases, control, communication, and metrology units are not clearly labeled, risking misidentification during checks .
- Space Constraints: Tight installations in urban areas often block access to rear panels, requiring dismantling and reassembly .
Case Study: A 2024 inspection at a local hospital revealed a DC pile with a metrology module embedded behind the cooling system, necessitating a 2-hour disassembly to verify its seal.
2.2 Environmental and Logistical Hurdles
Outdoor installations expose verification equipment to harsh conditions:
Environmental Factor | Impact on Verification | Occurrence Rate in Chifeng |
---|---|---|
Temperature extremes | Standard meters fail at >40°C or <0°C | 18% of summer/winter inspections |
Precipitation | Rainwater causes short circuits in connection ports | 12% of annual inspections |
Active Use by EV Drivers | Inability to disconnect piles during charging | 25% of peak-hour visits |
Inaccurate Location Data | GPS coordinates off by ≥500m in rural areas | 15% of township inspections |
Portable standard meters (costing ~¥50,000) offer flexibility but require manual transport of 20+ kg load banks, while 车载式 (vehicle-mounted) systems (£200,000+) struggle on unpaved roads .
2.3 Resource and Coordination Gaps
With only 3 certified verification teams in Chifeng, we face a 4:1 ratio of piles to technicians. Scheduling conflicts arise when:
- Operators delay bookings, causing seasonal backlogs (e.g., 500+ requests in Q4 2023).
- Multi-site operators (e.g., national charging networks) require cross-regional coordination, stretching staff capacity .
The E-CQS management system helps by prioritizing bookings, but manual data entry errors still occur in 5–8% of cases .
3. Innovations and Future Directions
To address these challenges, the metrology community is pivoting toward smarter, data-driven solutions:
3.1 Statistical Sampling Verification
Moving from 100% pile inspection to risk-based sampling, as tested in Wuhan’s EV Public Charging Infrastructure Metrology Supervision Specification . Key parameters include:
- Sample Size Calculation:\(n = \frac{Z^2 \cdot p \cdot (1-p)}{E^2}\) Where:
- \(Z =\) Z-score for confidence level (e.g., 1.96 for 95%)
- \(p =\) Expected failure rate (assumed 5%)
- \(E =\) Margin of error (2%) For 2000 piles, this yields \(n \approx 370\) samples, reducing workload by 81.5%.
3.2 Remote Data Acquisition
Piloting IoT-enabled systems to monitor real-time metrics:
- Key Monitored Parameters:ParameterFrequencyAccuracy RequirementVoltage/current10Hz±0.2% FSEnergy consumptionCumulative every 5min±0.5%Clock synchronizationDaily±5s/day
Early trials in Guangzhou showed that remote monitoring cut on-site visits by 40% for low-risk operators .
3.3 Anti-Cheating Technologies
Developing AI algorithms to detect anomalies in charging patterns, such as:
- Sudden spikes in energy loss (>3% vs. historical averages).
- Discrepancies between stated and actual charging speeds . Machine learning models trained on 50,000+ charging sessions achieved 92% accuracy in flagging potential fraud .
4. Strategic Recommendations
Based on field observations, I propose the following reforms:
- Standardized Design Guidelines: Mandate metrology-friendly layouts with ISO-compliant seal locations and labeled modules .
- Climate-Resilient Equipment: Invest in temperature-compensated standard meters (±0.1% error from -20°C to 60°C) and waterproof connectors.
- Collaborative Scheduling Platforms: Integrate E-CQS with operator APIs to auto-schedule verifications during low-use periods (e.g., 2–5 AM).
- Graded Certification System: Categorize operators into tiers (e.g., Platinum for <1% error rate) to prioritize high-risk sites.
Conclusion
EV charging pile verification is a critical yet evolving discipline. As the industry scales—with projections of 8 million public piles in China by 2030 —adopting statistical sampling, IoT monitoring, and collaborative governance will be essential. By bridging technical innovation with policy agility, we can ensure that every kilowatt-hour delivered is measured with precision, driving consumer confidence in the EV transition.