As a senior engineer specializing in traction battery standardization within the electric vehicle industry, the recent publication and implementation of GB/T 31486—2024, “Electrical performance requirements and test methods for traction battery of electric vehicle,” mark a significant evolution in the regulatory and testing landscape. This standard, effective since April 1, 2025, supersedes the 2015 version (GB/T 31486—2015) and addresses critical shifts in technology, operational understanding, and performance capabilities of traction batteries essential for modern electric vehicles. This analysis delves into the rationale, key revisions, technical specifications, and implications of this pivotal standard.
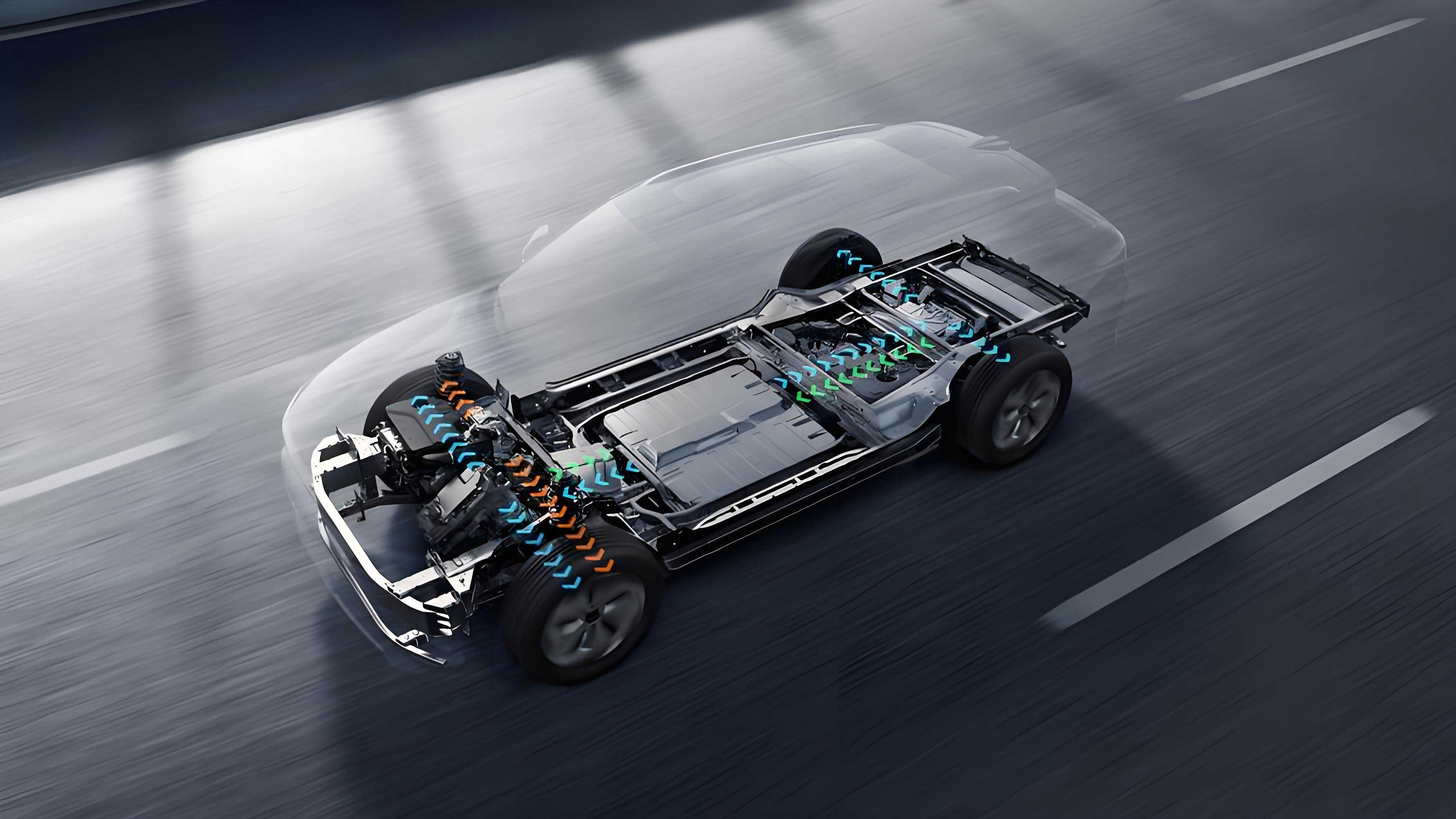
1. Introduction: The Imperative for Revision
Traction batteries are the cornerstone of electric vehicle performance, profoundly influencing safety, driving dynamics, and longevity. Parameters like capacity, energy density, temperature-dependent performance, rate capability, and charge retention directly dictate the user experience and vehicle viability. Standardized testing is paramount for fair product evaluation, reducing development costs, facilitating regulatory compliance (e.g., China’s New Energy Vehicle Enterprise and Product Access Management), and fostering industry innovation.
The 2015 standard established foundational requirements and test methods for modules and cells. However, rapid advancements rendered it partially obsolete:
- Structural Evolution (“Cell-to-Pack” – CTP Trend): The industry shift towards module-less (CTP) or cell-to-chassis (CTC) battery pack architectures diminished the relevance of module-centric testing.
- Enhanced Operational Understanding: Extensive real-world electric vehicle usage data provided deeper insights into actual battery operating conditions, revealing discrepancies with the 2015 test regimes.
- Performance Advancements: Traction battery performance has significantly surpassed the levels prevalent when the 2015 standard was drafted, necessitating stricter performance thresholds.
- System Standard Harmonization: The revision of the system-level performance standard GB/T 31467—2023 required alignment at the cell level.
Consequently, the National Technical Committee 114/Subcommittee 27 on Electric Vehicles initiated the revision in 2020, culminating in the 2024 publication.
2. Fundamental Revisions: Structure, Conditions, and Stringency
The 2024 standard introduces substantial changes across three primary dimensions:
2.1. Shift from Module to Cell Testing
Reflecting the CTP trend and aligning with international norms (IEC 62660-1:2018) and the cell-focused safety standard GB 38031—2020, the primary test object is now the individual battery cell. This directly links testing to the fundamental unit integrated into modern electric vehicle battery systems.
- Impact: Testing now more accurately reflects the performance of the actual battery units used in packs. Eliminates the artificial construct of “simulated modules” (often 1P5S) used under the 2015 standard.
- Increased Sample Size for Consistency: To rigorously evaluate cell-to-cell consistency – a critical factor for pack performance and longevity in electric vehicles – the number of test samples per sequence has been significantly increased. See Table 1.
Table 1: Comparison of Test Sample Requirements
Test Sequence | Test Item | GB/T 31486—2015 Samples | GB/T 31486—2024 Samples |
---|---|---|---|
1 | Appearance | Cells 1-10 | Cells 1-30 |
2 | Polarity | Modules 1-10 | |
3 | Mass & Dimensions | ||
4 | Room Temp. Discharge Capacity | Modules 1, 2 | Cells 1-5 |
5 | Room Temp. Rate Discharge Capacity | ||
6 | Room Temp. Rate Charge Performance | ||
7 | Low Temp. Discharge Capacity | ||
8 | High Temp. Discharge Capacity | Modules 3, 4 | Cells 6-10 |
9 | Room Temp. Charge Retention/Recovery | Modules 5, 6 | Cells 11-20 |
10 | High Temp. Charge Retention/Recovery | Module 7, 8 | – |
11 | Vibration Resistance | Modules 9, 10 | Cells 21-30 |
12 | Storage |
2.2. Optimization of Test Conditions Based on Real-World Electric Vehicle Operation
Test conditions have been refined using empirical data from electric vehicle fleets to ensure results better reflect actual usage scenarios.
- Discharge Rate Definitions: Analysis of driving cycles from various electric vehicles showed that over 90% of discharge and regen events occur at rates below 0.3C, with average discharge rates consistently under 0.3C (See conceptual Figs. 1 & 2 referenced in the standard). The 2015 standard’s reliance on the 1-hour rate (1I₁, where I₁ = Cₙ / 1h) for defining capacities was deemed unrepresentative.
- Revision: For High-Energy cells (defined as cells where Maximum Allowable Output Power / 1C Discharge Energy < 10), the standard capacity and energy ratings (Initial Capacity, Rated Capacity, Rated Energy) are now determined using the 3-hour rate discharge current (1I₃, where I₃ = Cₙ / 3h). High-Power cells (ratio ≥ 10) retain the 1I₁ definition. This change aligns capacity measurement with typical electric vehicle energy consumption profiles.
- Formula:
I₃ = Cₙ / 3
(where Cₙ is the rated capacity in Ah).
- Rate Discharge Currents: Real-world data indicated that the 2015 standard’s 3I₁ discharge rate for High-Energy cells was excessive (e.g., a high-energy electric vehicle at 160 km/h might only draw 0.7I₁).
- Revision: High-Energy cell rate discharge changed to 3I₃. Conversely, recognizing the higher demands on High-Power cells (common in hybrid electric vehicles), their rate discharge was increased to 10I₁. Current limits were also raised: 400A max removed for High-Energy; increased to 800A for High-Power.
- Rate Charge Methodology: The 2015 method (constant current (CC) charge at 2I₁ until voltage limit, max 400A, max 30 min) was problematic for large cells (>200Ah) and didn’t reflect real-world fast-charging strategies (often not pure CC).
- Revision: Allows manufacturer-defined charging protocols, provided the charge duration from 0% to the charge termination condition (SoC or voltage) is ≤ 30 minutes. The 400A limit is removed. Performance criteria (≥80% initial capacity recovery) remain.
- High-Temperature Conditions: Realistic thermal management in electric vehicles makes prolonged 55°C operation uncommon. Aligning with IEC 62660-1.
- Revision: High-temperature discharge, charge retention, and storage tests shifted from 55°C to 45°C.
- Environmental Adaptation: Fixed soak times (-20°C: 24h; 55°C: 5h) were inefficient and ineffective across diverse cell sizes.
- Revision: A dynamic termination criterion is introduced: Soak at target temperature until 1) Cell Temp – Ambient Temp ≤ 2°C, AND 2) Cell Temp change rate ≤ 1°C/h for ≥ 30 minutes (minimum 12h soak still required). This ensures thermal equilibrium is reliably achieved.
- Test Environment Tightening:
- Temperature: Changed from 25°C ±5°C to 25°C ±2°C (improves precision, aligns with GB/T 31467—2023 and equipment capabilities).
- Humidity: Changed from 15%~90% to 10%~90% (aligns with GB/T 31467—2023 and GB 38031—2020).
- Test Equipment (Wind Speed): Recognizing the significant impact of air velocity in thermal chambers on high/low-temperature performance results, a maximum wind speed of 1.7 m/s (per GB/T 10592—2008) is mandated. Fixtures/tooling are permitted to shield cells and minimize wind impact, provided they don’t contact the cell surface and cell orientation mimics the electric vehicle application.
- Data Logging: Increased resolution required:
- General Tests: Recording interval ≤ 100s (previously ≤ 1% of charge/discharge time).
- Rate Performance Tests: Recording interval ≤ 100ms (enables detailed transient analysis).
2.3. Enhanced Performance Requirements and Consistency Control
The 2024 standard significantly raises the bar for performance thresholds and introduces stricter consistency evaluation, pushing manufacturers to improve product quality and uniformity for electric vehicles.
Table 2: Key Performance Requirement Changes (Lithium-ion Examples)
Test Item | Test Object | Key Parameter Changes | GB/T 31486—2015 Requirement | GB/T 31486—2024 Requirement |
---|---|---|---|---|
Room Temp. Discharge Capacity | Cell | High-Energy: Discharge Rate 1I₁ → 1I₃ | ≥ Rated Cap., ≤ 110% Rated Cap. | ≥ Rated Cap., ≤ 110% Rated Cap. (All 30 samples) |
Room Temp. Rate Disch. Cap. | Cell | High-Energy: Rate 3I₁ → 3I₃; High-Power: Rate 8I₁ → 10I₁; Max Currents Raised | HE: ≥90% Init. Cap. HP: ≥80% Init. Cap. | HE: ≥95% Init. Cap. HP: ≥80% Init. Cap. |
Room Temp. Rate Chg. Perf. | Cell | Method: 2I₁ CC → Mfr. Protocol ≤30 min; Max 400A Removed | Disch. Cap. after chg. ≥80% Init. Cap. | Disch. Cap. after chg. ≥80% Init. Cap. |
Low Temp. Disch. Cap. (-20°C) | Cell | Discharge Rate adjusted per cell type (e.g., HE: 1I₁ → 1I₃) | ≥70% Init. Cap. | ≥70% Init. Cap. (Stricter due to cell vs. module) |
High Temp. Disch. Cap. | Cell | Temp: 55°C → 45°C; Discharge Rate adjusted per cell type | ≥90% Init. Cap. | ≥95% Init. Cap. |
Room Temp. Chg. Retention/Rec. | Cell | Soak Time: 28d → 30d | Retention ≥85% Init. Cap. Recovery ≥90% Init. Cap. | Retention ≥90% Init. Cap. Recovery ≥95% Init. Cap. |
High Temp. Chg. Retention/Rec. | Cell | Temp: 55°C → 45°C; Soak Time: 7d (unchanged); Added Energy Eff. | Retention ≥85% Init. Cap. Recovery ≥90% Init. Cap. | Retention ≥90% Init. Cap. Recovery ≥95% Init. Cap. Range (Ret, Rec, Eff) ≤5% |
Storage (45°C) | Cell | Soak Time: 28d → 30d; Added Energy Eff. | Recovery ≥90% Init. Cap. | Recovery ≥95% Init. Cap. Range (Rec, Eff) ≤5% |
Vibration Resistance | – | Deleted (Covered by GB 38031—2020; Not core electrical perf.) | No abnormal current/voltage | – |
- Consistency Requirements: A major addition is the explicit requirement for low cell-to-cell variation in specific tests:
- High-Temperature Charge Retention & Recovery: Range (Max-Min) of Retention Capacity, Recovery Capacity, and Energy Efficiency across all samples must be ≤ 5%.
- Storage: Range of Recovery Capacity and Energy Efficiency across all samples must be ≤ 5%.
- New Test Items: The standard introduces:
- Room Temperature Energy Efficiency
- High Temperature Energy Efficiency
- Rationale for Deletion (Vibration): Vibration testing was removed as it is primarily a mechanical/safety test, now adequately covered by GB 38031—2020, and not a core electrical performance characteristic.
3. Comparative Analysis with International Standards
While GB/T 31486—2024 sets performance requirements and test methods, the primary international standard, IEC 62660-1:2018, focuses solely on test methods for lithium-ion cells. Key differences:
- Scope: IEC 62660-1 is lithium-ion specific. GB/T 31486—2024, while primarily addressing lithium-ion due to market dominance, retains broader scope language.
- Performance Requirements: IEC 62660-1 defines no pass/fail criteria; GB/T 31486—2024 defines mandatory minimum performance levels.
- Specific Test Items: (See Table 3)
Table 3: Test Item Presence Comparison
Test Item | GB/T 31486—2024 | GB/T 31486—2015 | IEC 62660-1:2018 |
---|---|---|---|
Room Temp. Discharge Capacity | ✓ | ✓ | ✓ |
Room Temp. Discharge Energy | ✓ | ✓ | ✓ |
Room Temp. Specific Energy | ✓ | ✓ | ✓ |
Room Temp. Rate Discharge Capacity | ✓ | ✓ | ✓ |
Room Temp. Rate Charge Capacity | ✓ | ✓ | |
Power | ✓ | ||
Regenerative Power | ✓ | ||
Low Temp. Discharge Capacity | ✓ | ✓ | ✓ |
High Temp. Discharge Capacity | ✓ | ✓ | ✓ |
Room Temp. Charge Retention/Rec. | ✓ | ✓ | ✓ |
Room Temp. Energy Efficiency | ✓ | ||
High Temp. Charge Retention/Rec. | ✓ | ✓ | |
High Temp. Energy Efficiency | ✓ | ||
Storage | ✓ | ✓ | ✓ |
Vibration Resistance | ✓ |
- Power Testing: GB/T 31486—2024 excludes power and regenerative power tests. The rationale is twofold: 1) Power targets are highly application-specific (dependent on the electric vehicle design), making unified pass/fail criteria impractical; 2) Power test methodology is covered in the separate Chinese industry standard QC/T 1227 (under approval).
- Harmonization Efforts: Despite differences, GB/T 31486—2024 demonstrates conscious alignment with IEC 62660-1:2018 in areas like high-temperature test conditions (45°C) and the core definition of discharge capacity (using standardized rates).
4. Impact and Significance for the Electric Vehicle Industry
The implementation of GB/T 31486—2024 carries substantial implications:
- Enhanced Relevance and Accuracy: Testing now aligns with CTP battery structures and actual electric vehicle operating profiles, yielding results more reflective of real-world performance.
- Higher Product Quality Bar: Stricter performance thresholds (e.g., 95% vs 90% for HE rate discharge, 95% vs 90% for storage recovery) and mandatory consistency controls will drive manufacturers to improve fundamental cell performance and production process control. This directly benefits electric vehicle reliability, range, and longevity.
- Streamlined Development and Certification: The shift to cell-level testing simplifies R&D validation and type approval processes for battery suppliers and electric vehicle manufacturers, eliminating the need for artificial module constructs.
- Stronger Regulatory Foundation: As a referenced standard in China’s electric vehicle access management, the updated requirements ensure new vehicles utilize higher-performance, more consistent battery technology.
- Promotion of Technological Advancement: By raising the bar, the standard incentivizes innovation in cell chemistry, design, and manufacturing to meet the tougher criteria, accelerating the advancement of electric vehicle battery technology.
5. Future Directions for Traction Battery Performance Standards
While GB/T 31486—2024 represents a significant step forward, further evolution is needed to support the rapidly advancing electric vehicle sector:
- Performance Grading Standards: The current standard defines minimum (“access-level”) requirements. Developing hierarchical performance grading standards (e.g., Bronze, Silver, Gold) would incentivize manufacturers to develop and market premium cells exceeding the baseline, providing clearer differentiation for high-performance electric vehicles.
- Robust Power Characterization: Despite its exclusion from GB/T 31486, accurate and repeatable measurement of internal resistance and power capability (HPPC, pulse power) remains crucial for electric vehicle design, battery management, and state-of-health estimation. Standardizing methods resistant to instrumentation error and thermal influences is a critical challenge, especially as cell resistances decrease.
- Whole-Life-Cycle Performance Assessment: Current standards focus on “fresh” cells. Developing validated methods to assess the electrical performance of batteries throughout their operational life within an electric vehicle and in secondary applications (e.g., stationary storage) is essential for predicting lifespan, enabling effective warranties, and determining residual value for reuse/recycling. Techniques like Distribution of Relaxation Times (DRT) analysis show promise.
6. Conclusion
GB/T 31486—2024 is a critical update that modernizes the evaluation framework for traction battery electrical performance in electric vehicles. By transitioning to cell-level testing, rigorously optimizing test conditions based on real-world electric vehicle data, significantly elevating performance thresholds, and introducing stringent consistency requirements, the standard sets a higher benchmark for product quality and reliability. It aligns more closely with technological trends (CTP), international methods (IEC), and system-level standards (GB/T 31467.3), while eliminating redundant tests. The implementation of this standard will undoubtedly propel improvements in cell technology and manufacturing consistency, providing essential support for the safety, performance, and sustainable growth of the global electric vehicle industry. Future work on performance grading, power characterization, and life-cycle assessment will be vital to maintain the standard’s relevance and continue driving innovation in electric vehicle battery technology.