Introduction As a researcher deeply engaged in the development of electric vehicle (EV) technologies, I have dedicated significant effort to analyzing the advancements in distributed drive systems. These systems, which directly integrate drive motors into the wheels, offer unprecedented flexibility in power distribution and vehicle control. In this paper, I will elaborate on key technical aspects of distributed drive systems, including motor cooling methods, control strategies, electronic differential systems, differential steering mechanisms, and chassis integrated control, all of which are critical for enhancing EV performance, efficiency, and safety.
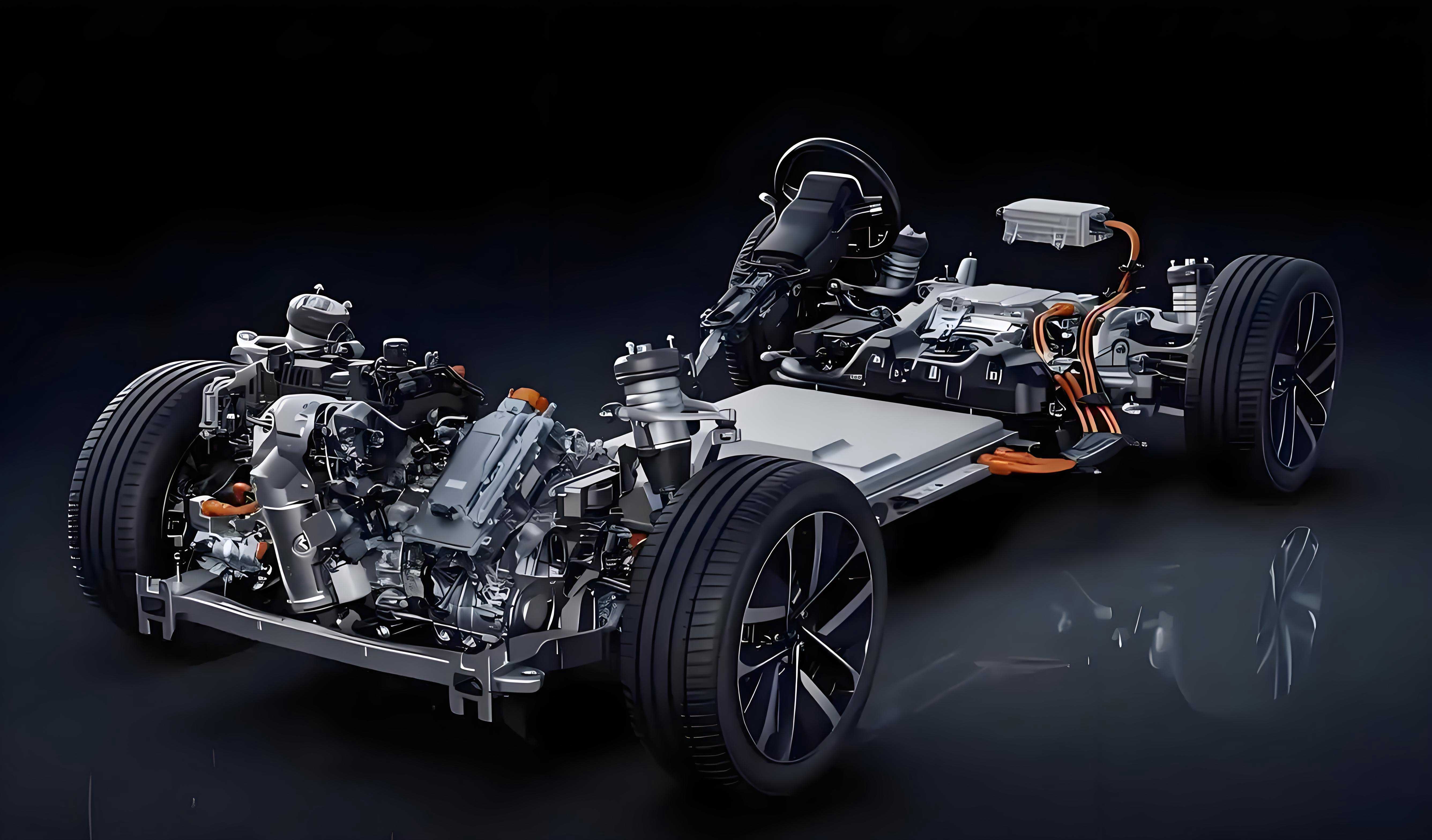
1. Cooling Methods for Hub Motors
In the design of permanent magnet hub motors, cooling efficiency is pivotal for maintaining temperature stability and reliability. Two primary cooling methods are widely employed, each with distinct characteristics tailored to different power requirements and operational scenarios.
1.1 Air Cooling
Air cooling is a prevalent choice for low-power motors due to its simplicity and cost-effectiveness. This method relies on air flow generated during motor operation to dissipate heat. Forced air cooling systems, as illustrated in Figure 1, incorporate internal fans and rotor ventilation ducts to circulate air through the stator-rotor gap and heat dissipation fins on the casing. The airflow absorbs heat from the motor components and releases it to the environment, creating a continuous cooling cycle.
Advantages:
- Low cost and simple structure.
- Easy installation and maintenance.
- High reliability for low-power applications.
Disadvantages:
- Limited heat dissipation capacity compared to liquid cooling.
- Unsuitable for high-power density motors, as it struggles to manage excessive heat generation .
Table 1: Key Parameters of Forced Air Cooling Systems
Parameter | Description |
---|---|
Heat Transfer Mechanism | Convection via forced air flow through ventilation ducts and heat fins. |
Cooling Efficiency | Dependent on fin geometry, airflow rate, and surface heat transfer coefficient. |
Typical Applications | Small-scale EVs and low-power auxiliary motors. |
1.2 Liquid Cooling
For high-power hub motors, liquid cooling (water or oil) is essential to manage higher heat loads. This method utilizes liquids with superior thermal conductivity to absorb and transfer heat more effectively than air.
1.2.1 Water Cooling
Water cooling is widely adopted for its high heat capacity and low cost. Common designs involve integrating spiral or “Z”-shaped water channels into the motor casing to directly cool the stator yoke and winding ends. For example, a typical water-cooling system (Figure 2) circulates a coolant mixture (often water with antifreeze) through these channels, absorbing heat and transferring it to an external radiator.
Advantages:
- High cooling efficiency, suitable for high-power density motors.
- Low cost and environmental friendliness.
Disadvantages:
- Complex structure requiring pumps, radiators, and seals.
- Vulnerable to freezing in cold climates and scaling from mineral deposits.
- Requires regular maintenance to prevent corrosion .
Table 2: Comparison of Water Channel Designs
Design Type | Inlet/Outlet Placement | Flow Resistance | Temperature Distribution |
---|---|---|---|
Circumferential Spiral | Ends of the motor | Low | Gradient between motor ends |
Circumferential “Z” Shape | Same end | High | More uniform temperature |
1.2.2 Oil Cooling
Oil cooling involves filling the motor cavity with heat-conductive oil, which is agitated by the rotor to carry heat from the windings and permanent magnets to the casing. The oil’s viscosity, however, creates drag on the rotor, making this method unsuitable for high-speed applications.
Advantages:
- Excellent heat dissipation for low-to-medium speed motors.
- Reduces mechanical wear by lubricating moving parts.
Disadvantages:
- High viscous resistance at high speeds.
- Complex oil management and potential leakage risks .
Equation 1: Heat Dissipation Rate in Liquid Cooling\(Q = h \cdot A \cdot \Delta T\) Where:
- Q: Heat transfer rate (W),
- h: Heat transfer coefficient (W/m²K),
- A: Heat transfer area (m²),
- \(\Delta T\): Temperature difference (K).
2. Hub Motor Control Strategies
Effective control of hub motors is critical for minimizing torque ripple, reducing vibration, and improving overall driving comfort. Two primary challenges are addressed through innovative control algorithms: torque pulsation and unbalanced magnetic pull.
2.1 Reducing Torque Pulsation
Torque pulsation in hub motors arises from cogging torque (due to stator-rotor magnetic interaction) and commutation torque ripple. To mitigate this, we employ a dual approach: motor design optimization and control parameter compensation.
Control Methods:
- Parameter Correction: Adjusting motor inductance, resistance, and flux linkage values in real-time to compensate for torque fluctuations.
- Multi-Field Coupling Control: Integrating electromagnetic, thermal, and stress field models to predict and suppress torque variations under dynamic loads .
Equation 2: Cogging Torque Formula\(T_{cog} = -\frac{1}{2} \cdot N \cdot \Phi^2 \cdot \frac{d \Lambda}{d\theta}\) Where:
- N: Number of poles,
- \(\Phi\): Magnetic flux,
- \(\Lambda\): Reluctance,
- \(\theta\): Rotor position angle.
2.2 Suppressing Unbalanced Magnetic Pull (UMP)
UMP occurs when stator-rotor eccentricity creates uneven magnetic fields, leading to vibration and reduced component lifespan. Control strategies focus on:
- Active Magnetic Bearing Control: Using feedback algorithms to adjust motor currents and counteract radial forces.
- Optimal Current Vector Control: Modifying conduction angles and current waveforms to minimize radial magnetic forces .
Table 3: Impact of UMP on Motor Performance
Parameter | Low UMP | High UMP |
---|---|---|
Vibration Amplitude | <5 mm/s | >15 mm/s |
Noise Level | <65 dB(A) | >80 dB(A) |
Bearing Life | >10,000 hours | <5,000 hours |
3. Electronic Differential System (EDS) for Distributed EVs
Unlike traditional vehicles with mechanical differentials, distributed EVs rely on electronic differential systems to manage wheel speed differences during turns or uneven terrain. EDS ensures smooth cornering by independently controlling each wheel’s speed, eliminating tire slip and improving stability.
3.1 Role of the Differential
In traditional vehicles, mechanical differentials (e.g., bevel gear systems) allow wheels to rotate at different speeds during turns. In distributed EVs, while each wheel is independently driven, improper torque distribution can still cause slip or skid. EDS addresses this by calculating target speeds based on the Ackermann steering model:\(\frac{V_{outer}}{V_{inner}} = \frac{R + B/2}{R – B/2}\) Where:
- \(V_{outer}\): Speed of the outer wheel,
- \(V_{inner}\): Speed of the inner wheel,
- R: Turning radius,
- B: Track width .
3.2 Control Methods for EDS
Two primary control strategies are used to achieve differential steering:
3.2.1 Speed Control Method
This approach uses the Ackermann model to set target speeds for each wheel and employs PID controllers for closed-loop speed regulation. While effective for basic differential needs, it struggles with torque stability, as independent wheel control can lead to overall power fluctuations .
3.2.2 Slip Ratio Control Method
By maintaining wheel slip ratios within an optimal range (typically 10–20%), this method balances traction and stability. The slip ratio \(\lambda\) is calculated as:\(\lambda = \frac{v – \omega \cdot r}{v} \times 100\%\) Where:
- v: Vehicle speed,
- \(\omega\): Wheel angular velocity,
- r: Tire radius.
Advantages:
- Prevents wheel spin and improves grip on low-friction surfaces.
- More robust than speed control in dynamic scenarios .
Table 4: Comparison of EDS Control Strategies
Aspect | Speed Control | Slip Ratio Control |
---|---|---|
Control Objective | Wheel speed matching | Slip ratio optimization |
Stability | Moderate | High |
Complexity | Low | High |
Application Scenario | Dry, flat roads | Wet, icy, or uneven terrain |
4. Differential Steering for Distributed EVs
Differential Drive Assist Steering (DDAS) is a groundbreaking technology that uses torque differences between left and right wheels to assist steering, eliminating the need for traditional hydraulic or electric power steering systems.
4.1 Basic Principle of DDAS
When unequal torques are applied to the front wheels, a steering moment is generated around the kingpin axis. This moment, combined with the driver’s input, reduces steering effort and improves maneuverability. The differential steering torque \(T_d\) is given by:\(T_d = (F_{left} – F_{right}) \cdot e\) Where:
- \(F_{left/right}\): Drive forces on left/right wheels,
- e: Kingpin offset distance .
Advantages of DDAS:
- Reduced mechanical complexity and cost by eliminating power steering components.
- Lower noise and improved energy efficiency.
- Enhanced maneuverability through torque-induced steering assistance .
4.2 Coordinated Control with Active Steering
In low-traction conditions, DDAS alone may struggle to maintain precise steering control. To address this, a coordinated control system integrates DDAS with active steering (AS), which adjusts wheel angles in real-time based on vehicle dynamics:
- Understeer Compensation: AS increases front wheel angle to counteract insufficient turning.
- Oversteer Compensation: AS reduces front wheel angle to stabilize rear-wheel slip .
Figure 1: Coordinated Control Block Diagram
plaintext
Steering Wheel Input → DDAS Controller → Torque Difference Calculation → Wheel Motors
↘ AS Controller → Wheel Angle Adjustment → Steering Mechanism
Table 5: Performance Comparison of Steering Systems
Feature | Traditional EPS | DDAS Alone | DDAS + AS |
---|---|---|---|
Steering Effort | Moderate | Low | Very low |
High-Speed Stability | Good | Good | Excellent |
Low-Traction Performance | Poor | Moderate | Excellent |
System Complexity | High | Low | Moderate |
5. Chassis Integrated Control for EVs
Modern EV chassis control systems integrate multiple subsystems to optimize vehicle dynamics, safety, and comfort. These systems are categorized into four domains: braking, suspension, steering, and drive control, as outlined in Table 6.
Table 6: Classification of Chassis Control Systems
Domain | Subsystems | Key Functions |
---|---|---|
Braking | ABS, EBD, ESC, Regenerative Braking | Prevent lockup, distribute braking force, stabilize during evasive maneuvers. |
Suspension | Active Suspension, Continuous Damping Control | Reduce body roll, improve ride comfort on uneven roads. |
Steering | Active Front Steering, Four-Wheel Steering | Enhance maneuverability and high-speed stability. |
Drive | Traction Control, Four-Wheel Drive | Optimize power distribution and prevent wheel spin. |
5.1 Integrated Control Strategy
An integrated chassis control system (ICCS) coordinates these subsystems to address complex driving scenarios. For example, during emergency braking on a split-friction road, ICCS may:
- Activate ABS to prevent wheel lockup.
- Use ESC to apply differential braking forces.
- Adjust suspension damping to maintain vehicle balance.
- Modify drive torque distribution to stabilize the vehicle .
Equation 3: Vehicle Dynamics Model for ICCS\(\sum F_x = m \cdot \dot{u} + m \cdot v \cdot r\)\(\sum F_y = m \cdot \dot{v} – m \cdot u \cdot r\)\(\sum M_z = I_z \cdot \dot{r}\) Where:
- \(u, v\): Longitudinal and lateral velocities,
- r: Yaw rate,
- \(I_z\): Moment of inertia about the z-axis.
5.2 Challenges in Integrated Control
- Multi-Objective Optimization: Balancing conflicting goals (e.g., comfort vs. stability).
- Real-Time Data Fusion: Processing sensor data from multiple subsystems (e.g., wheel speed, yaw rate, steering angle) with minimal latency.
- Robustness: Ensuring reliable operation across diverse road conditions and vehicle loads .
6. Conclusion
As a key contributor to the advancement of electric vehicle technology, distributed drive systems have revolutionized how we approach motor design, vehicle control, and chassis integration. Through innovative cooling solutions, precise motor control algorithms, intelligent electronic differentials, and adaptive steering mechanisms, we have significantly enhanced EV performance, efficiency, and safety.
Looking ahead, the integration of artificial intelligence and machine learning will further optimize these systems, enabling real-time adaptation to dynamic driving environments. As researchers and engineers, our continued focus on refining these technologies will be pivotal in driving the EV industry toward a future of sustainable, high-performance mobility.
Keywords: electric vehicle, distributed drive, hub motor, cooling system, electronic differential, differential steering, chassis control
Appendix: Nomenclature
Symbol | Description | Unit |
---|---|---|
Q | Heat transfer rate | W |
h | Heat transfer coefficient | W/m²K |
\(\lambda\) | Wheel slip ratio | % |
\(T_d\) | Differential steering torque | N·m |
r | Yaw rate | rad/s |
\(I_z\) | Moment of inertia | kg·m² |
This comprehensive overview highlights the multifaceted nature of distributed drive technologies and their pivotal role in shaping the future of electric vehicles. By addressing technical challenges through innovative design and control strategies, we continue to push the boundaries of what is achievable in sustainable transportation.